Since there isn't a filler section of this website (understandable since SPI isn't in the filler business) I decided to post this here as the SPI forums are full of peop;le that give the best advice...
Most of the panels on my car are new so I won't have any thick filler , EXCEPT, over where the factory lead joints originally were at the top of the 1/4 where it meets the roof, and at the back of the 1/4 where it meets the trunk transition panel. I don't have the skills of Rusty and Brian to weld patches over those areas like they did on their 65-66 fastback. The filler I have been using is Rage Gold Extreme, could I use it over those joints?
Should I get something different for there, or do I need to try to weld something in?
Here is the trunk transition to 1/4 joint:
Here is the roof joint before I plug welded (while test fitting the rear window):
Most of the panels on my car are new so I won't have any thick filler , EXCEPT, over where the factory lead joints originally were at the top of the 1/4 where it meets the roof, and at the back of the 1/4 where it meets the trunk transition panel. I don't have the skills of Rusty and Brian to weld patches over those areas like they did on their 65-66 fastback. The filler I have been using is Rage Gold Extreme, could I use it over those joints?
Should I get something different for there, or do I need to try to weld something in?
Here is the trunk transition to 1/4 joint:
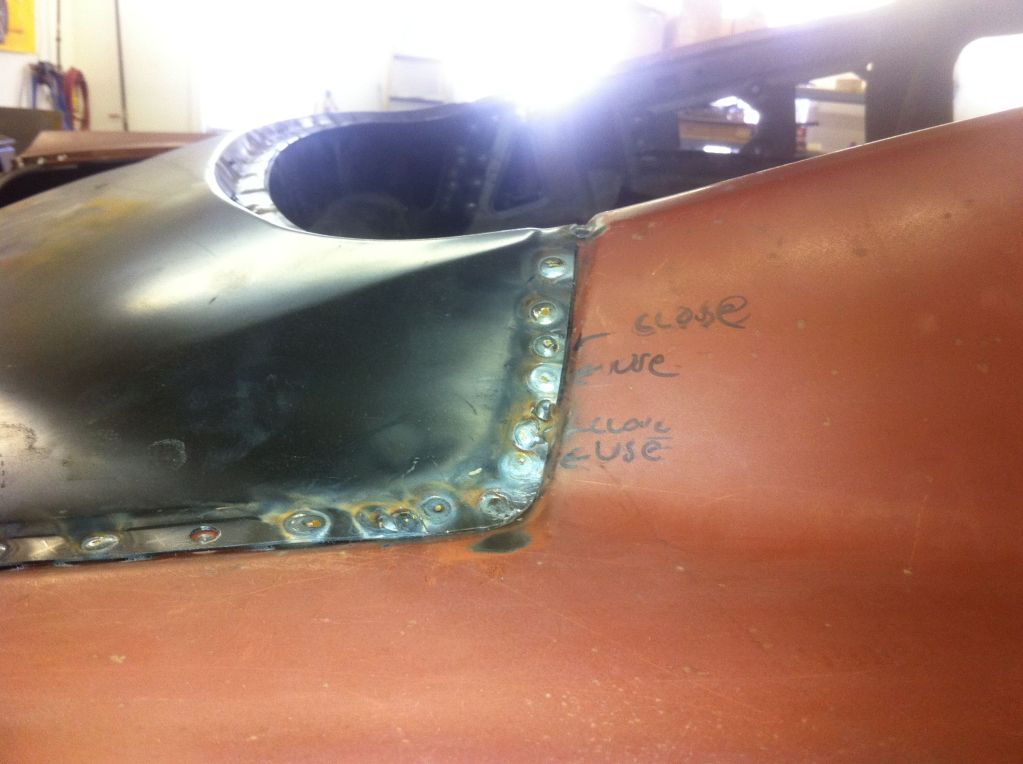
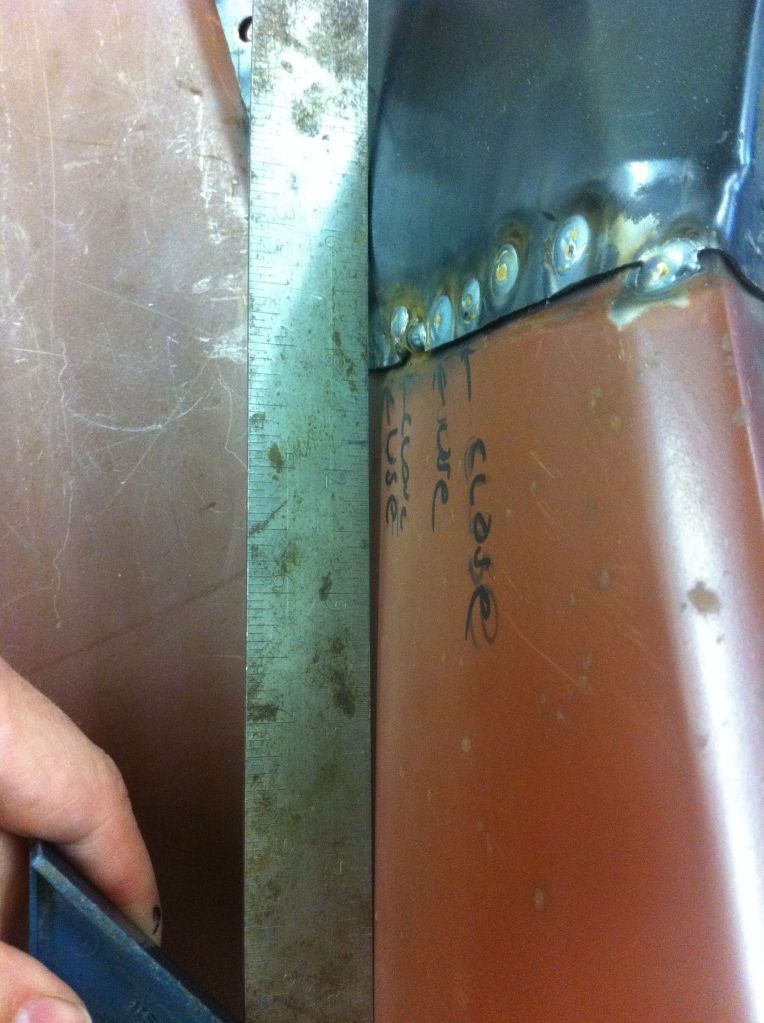
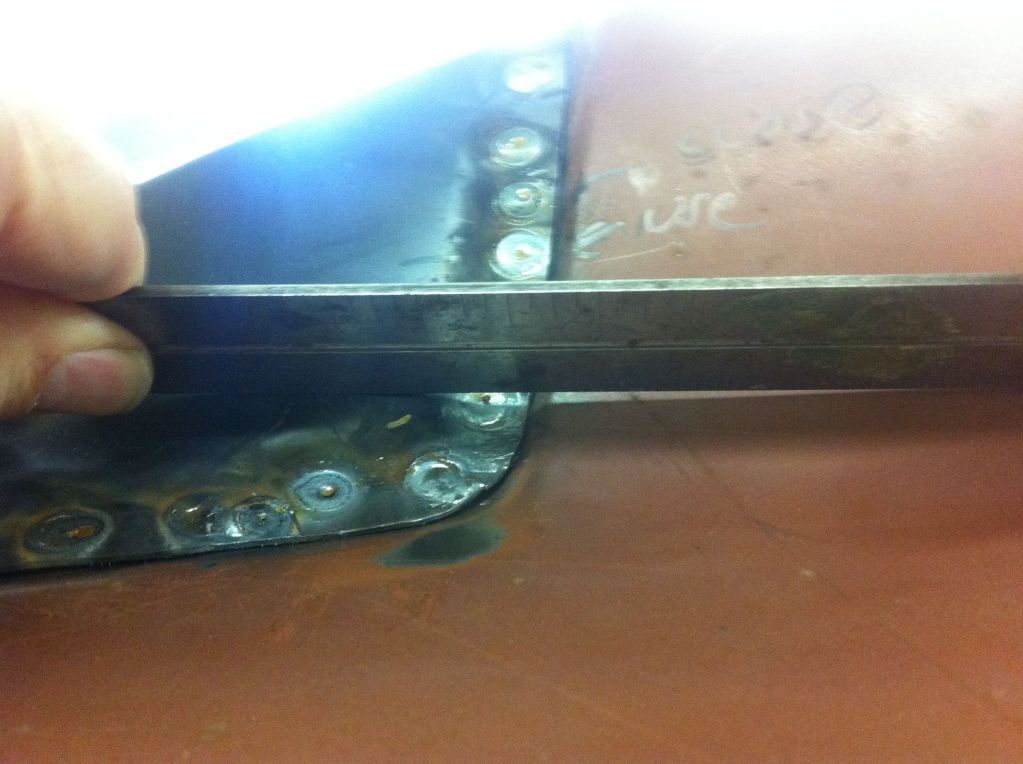
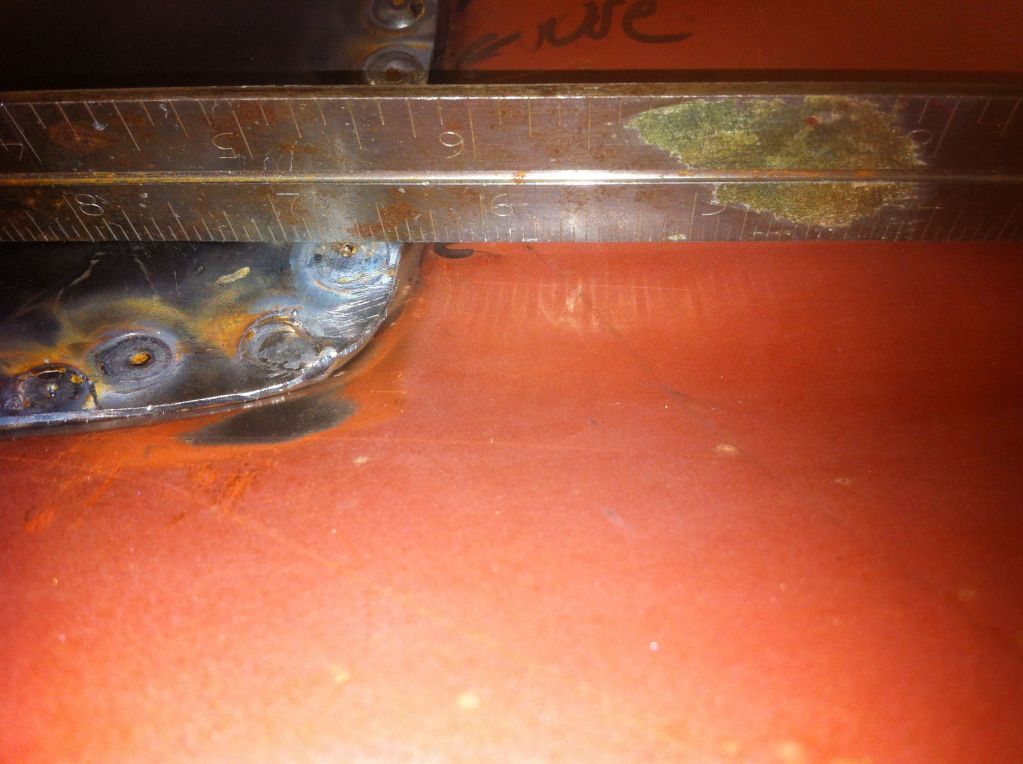
Here is the roof joint before I plug welded (while test fitting the rear window):
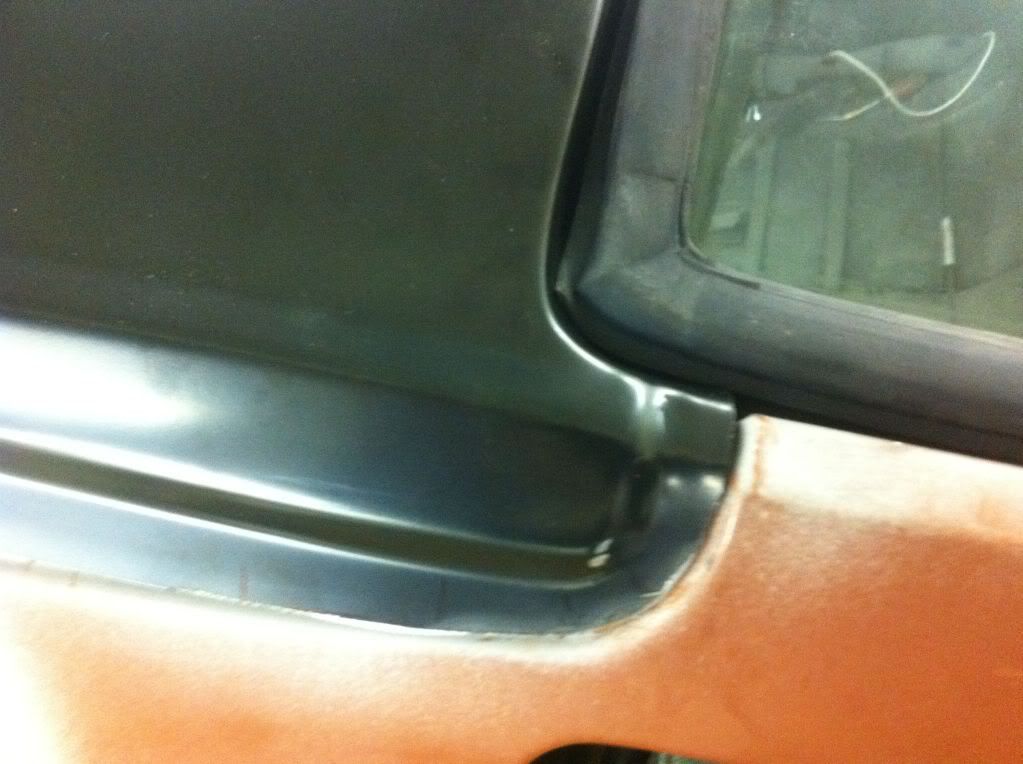