Mitch
Promoted Users
Since my avatar pic is obviously a car in resto, I thought I would share a little about it. I bought this Camaro in about 2008 as a basket case. It was in Spring Valley WI and had been brought up there from the San Fran area and blown apart for a resto that didn't happen.
I was told by the seller that it had been a driver before he blew it apart, so I had the big idea I would reassemble it and drive it for a while before restoring it. So 2 weeks later, I drove it out of the shop. Still needed a lot of work to be decent, but it was a "driver" again.
I repainted the metal door sills, put in new carpet, repaired the lower door panels and bought a pair of nice, standard, seats. It stayed like this until 5 years ago.
The trunk floor was badly rusted out and had crash damage in the right rear corner that was never straightened very well. The right quarter had a section brazed on over some of the remaining original quarter and the tail panel was sectioned on thru the left tail light. These would be replaced later. For now, I was replacing the entire trunk floor with an AMD 1 piece. Dropped the rear axle and fuel tank and got going with the plasma cutter.
Original paint under the filler neck, Granada Gold, which it is going back to.
I worked part time at a major collision repair shop, but in the back room doing restoration work. I was fortunate to be able to borrowed a set of gauges and tram to get the floor installed correctly.
This poor car had been smacked around multiple times and this was one of the "neat" bondo repairs it had done to it.
Long story, short version, I did many small repairs and "adjustments" along the way to replacing the floor as well as most of the left inner wheel house.
Prepped and pre-drilled to weld to the frame rails and drops.
Fitting the wheel house.
All measured, aligned, clamped and ready to weld
And the welding fun begins.
My shop driveway March 9 2019. We got 2" of rain and that is 300 ft of ice slide to the road. The culvert was frozen and the ditch flooded and overran the driveway, washing out the gravel. What a fun 2 days that was cleaning up that mess... anyway, back to the program.
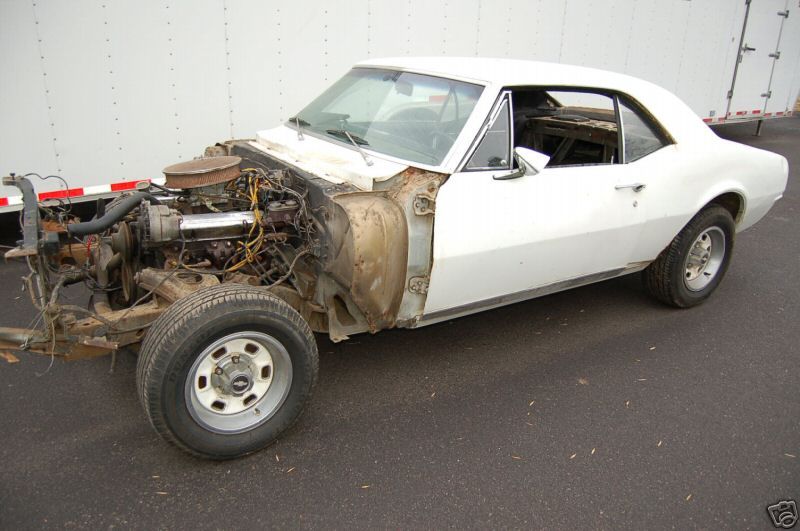
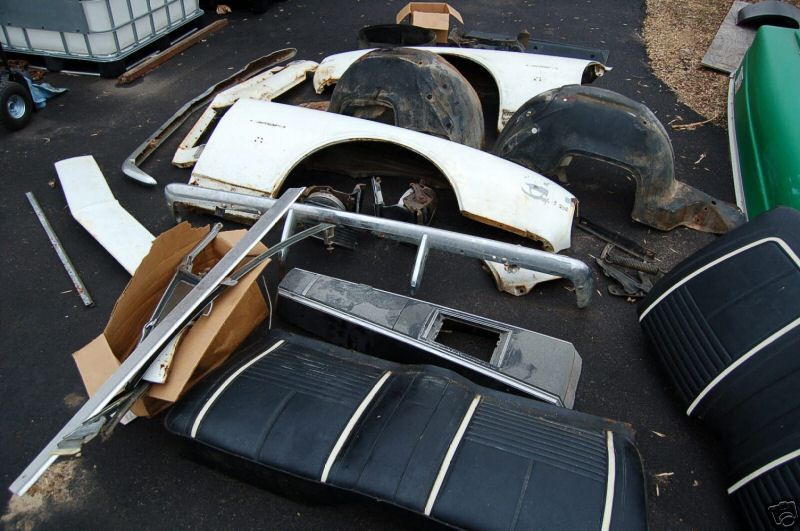
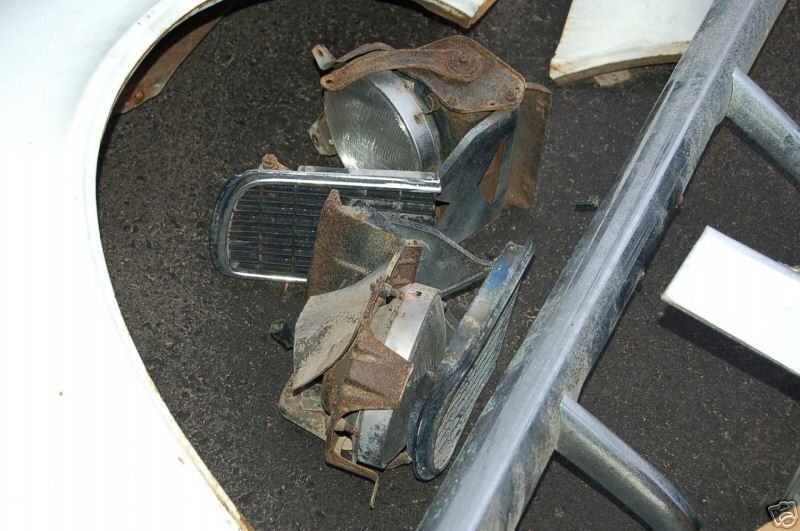
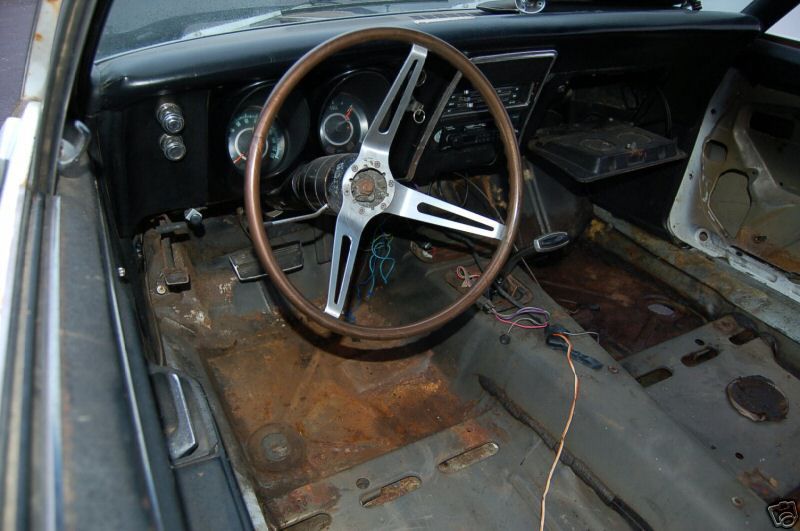
I was told by the seller that it had been a driver before he blew it apart, so I had the big idea I would reassemble it and drive it for a while before restoring it. So 2 weeks later, I drove it out of the shop. Still needed a lot of work to be decent, but it was a "driver" again.
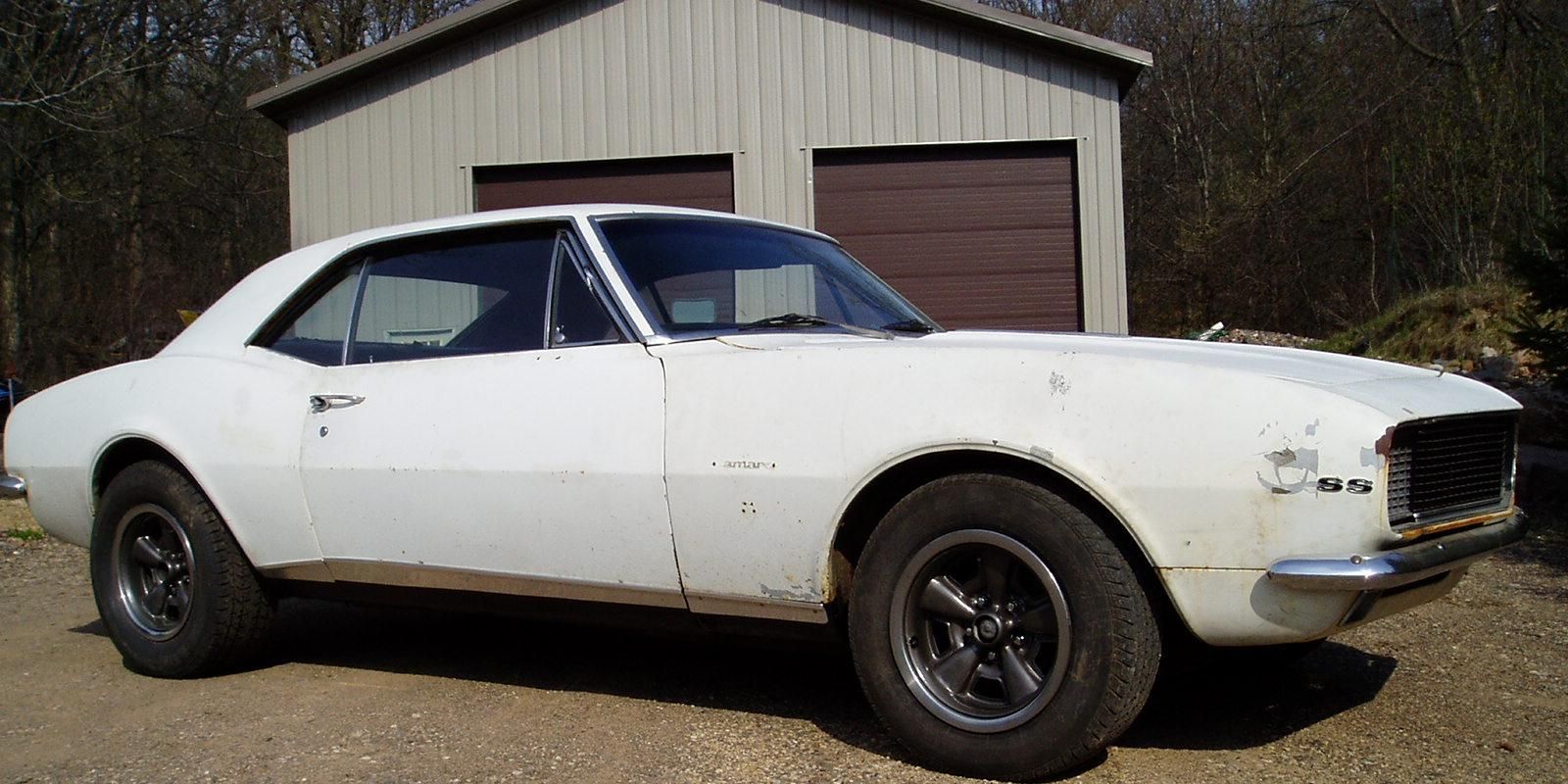
I repainted the metal door sills, put in new carpet, repaired the lower door panels and bought a pair of nice, standard, seats. It stayed like this until 5 years ago.
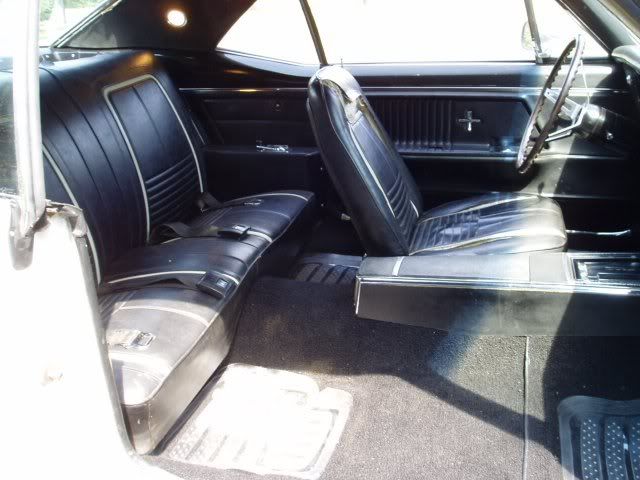
The trunk floor was badly rusted out and had crash damage in the right rear corner that was never straightened very well. The right quarter had a section brazed on over some of the remaining original quarter and the tail panel was sectioned on thru the left tail light. These would be replaced later. For now, I was replacing the entire trunk floor with an AMD 1 piece. Dropped the rear axle and fuel tank and got going with the plasma cutter.
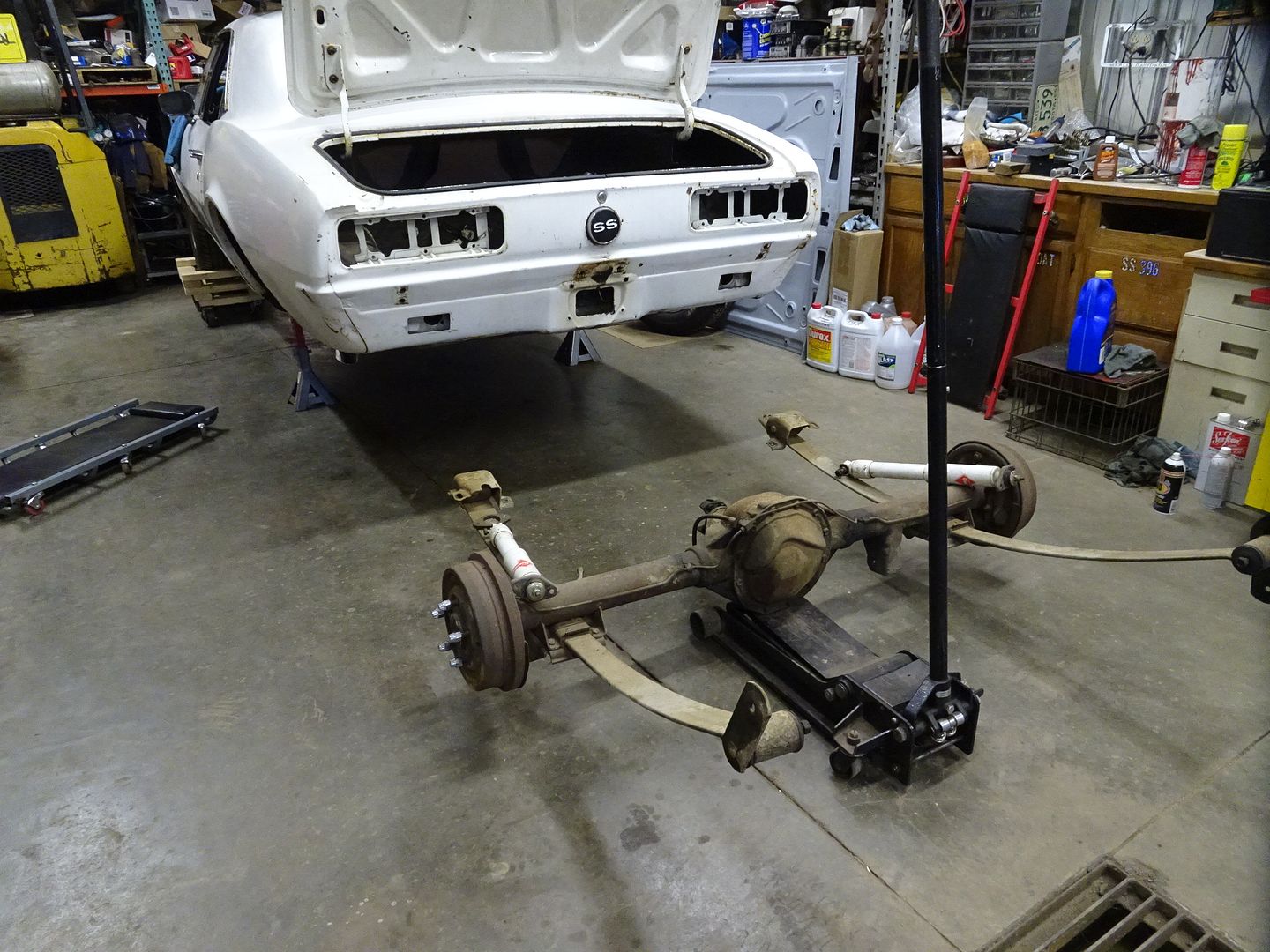
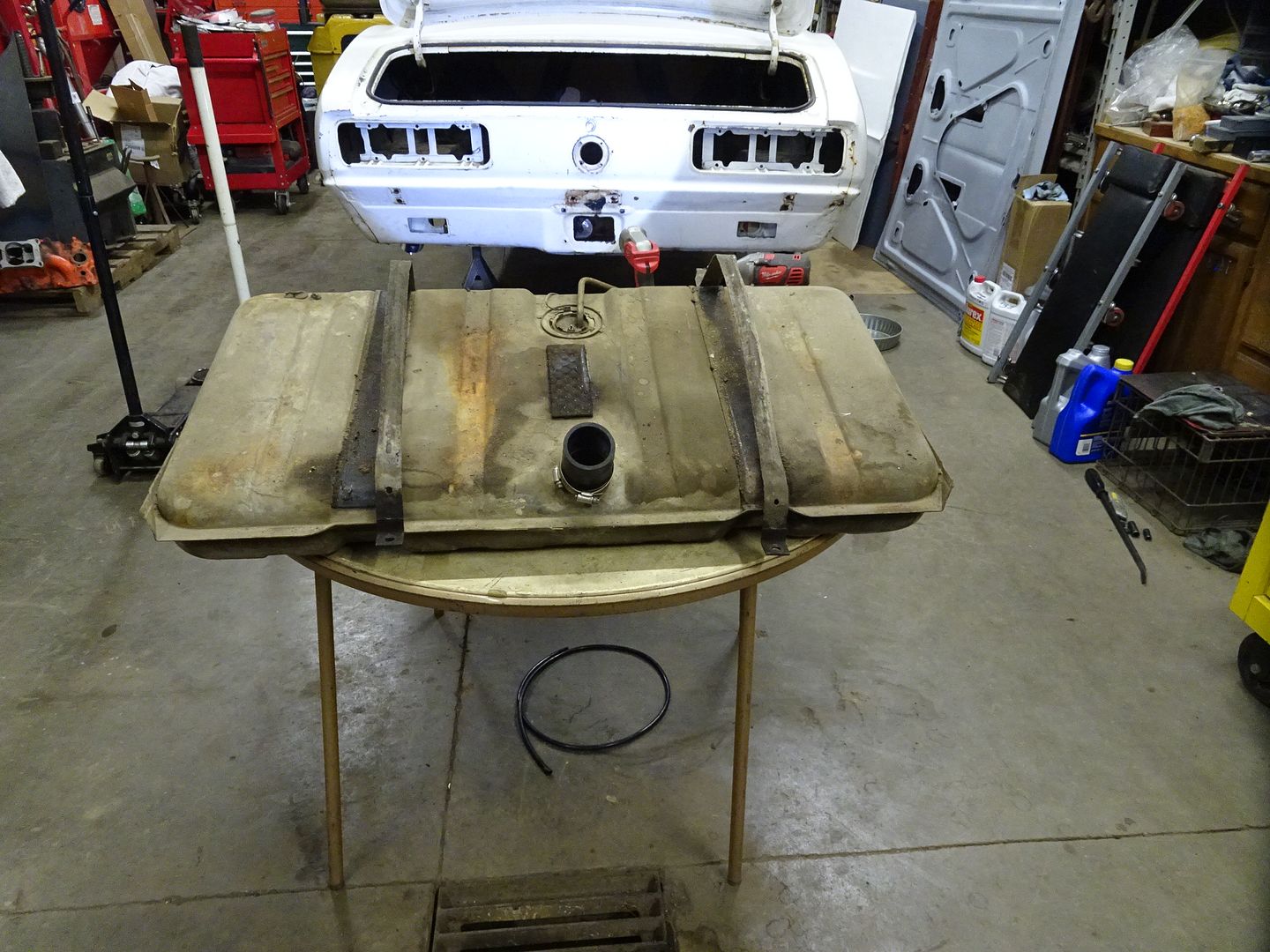
Original paint under the filler neck, Granada Gold, which it is going back to.
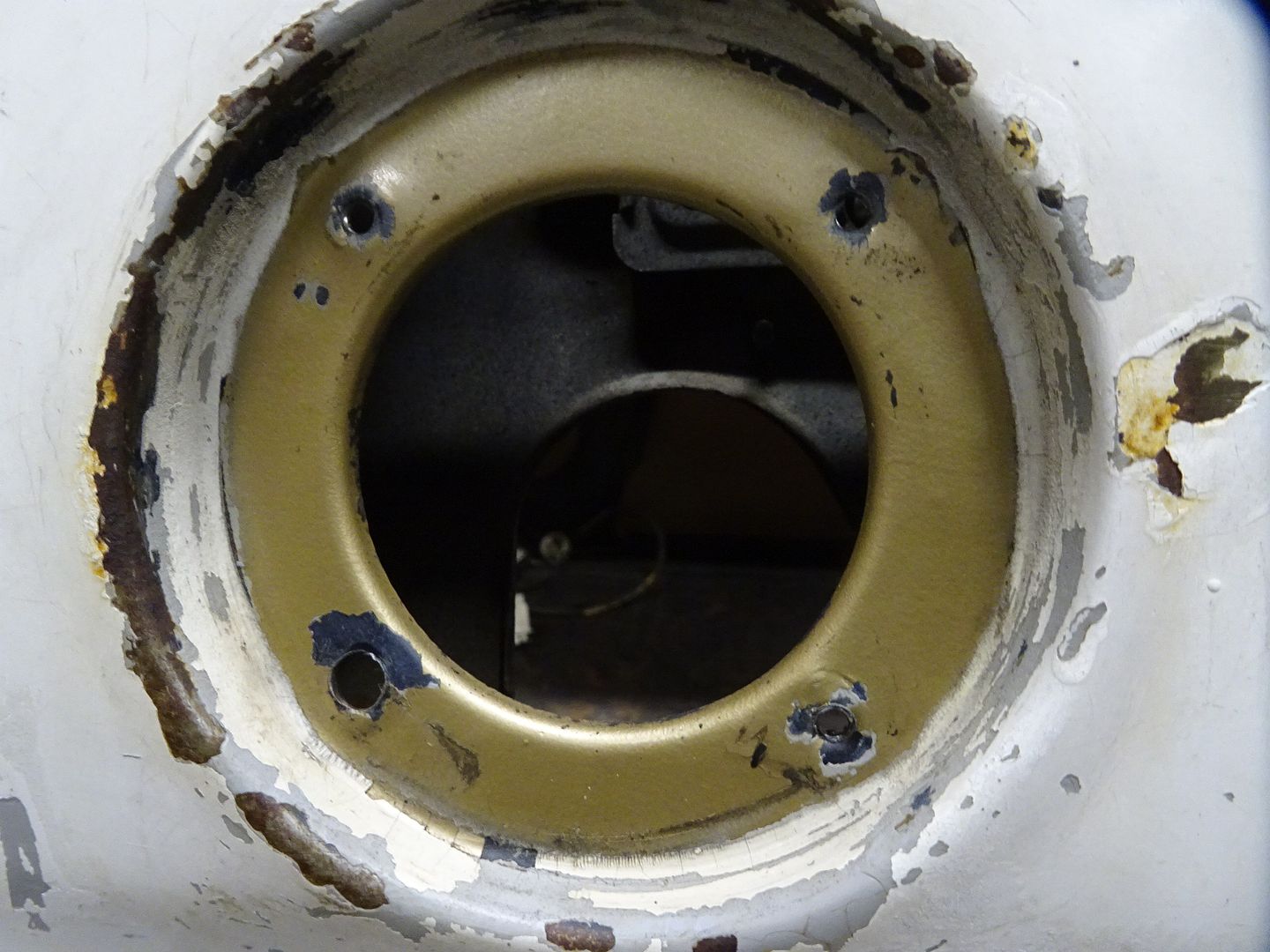
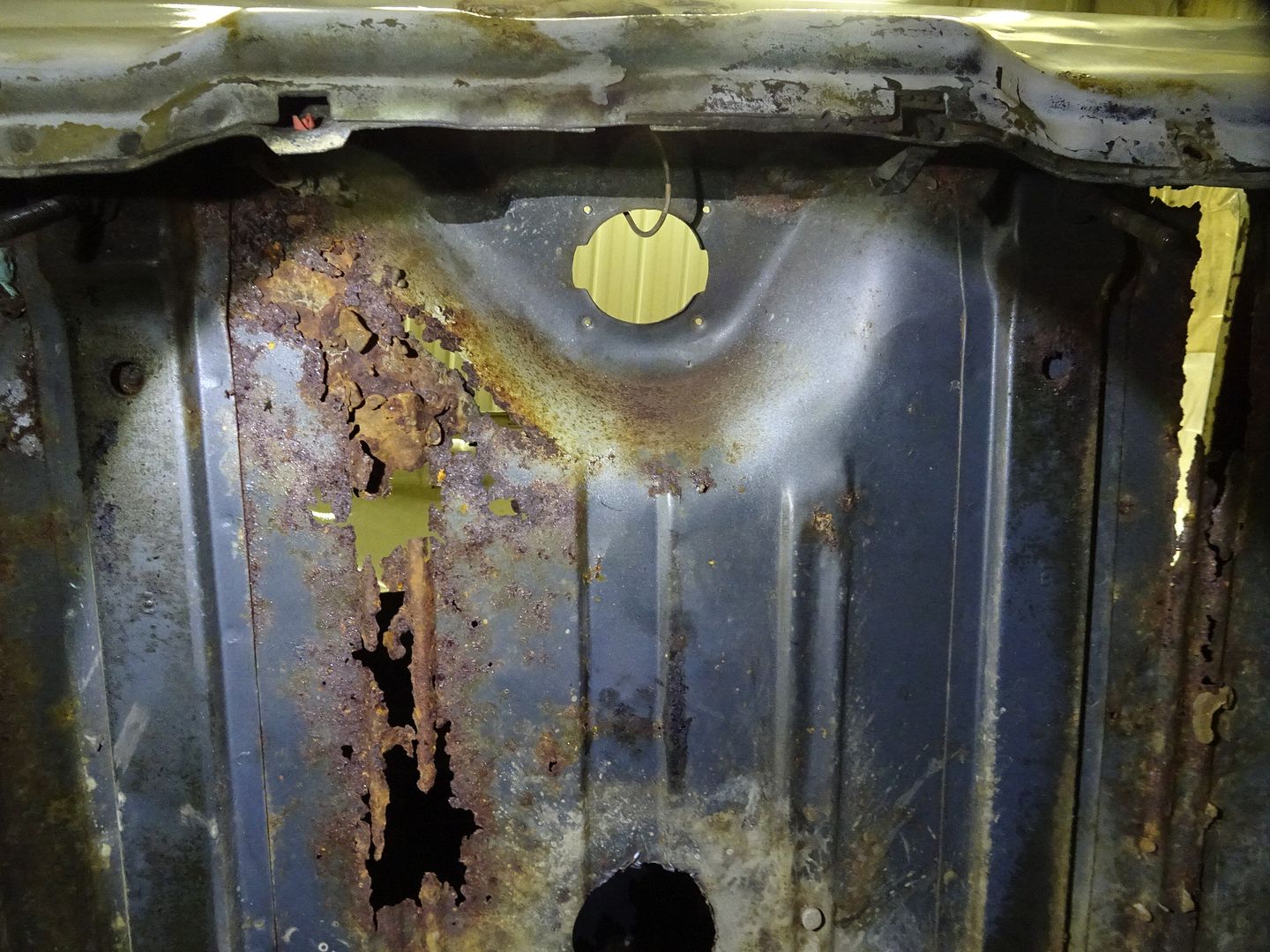
I worked part time at a major collision repair shop, but in the back room doing restoration work. I was fortunate to be able to borrowed a set of gauges and tram to get the floor installed correctly.
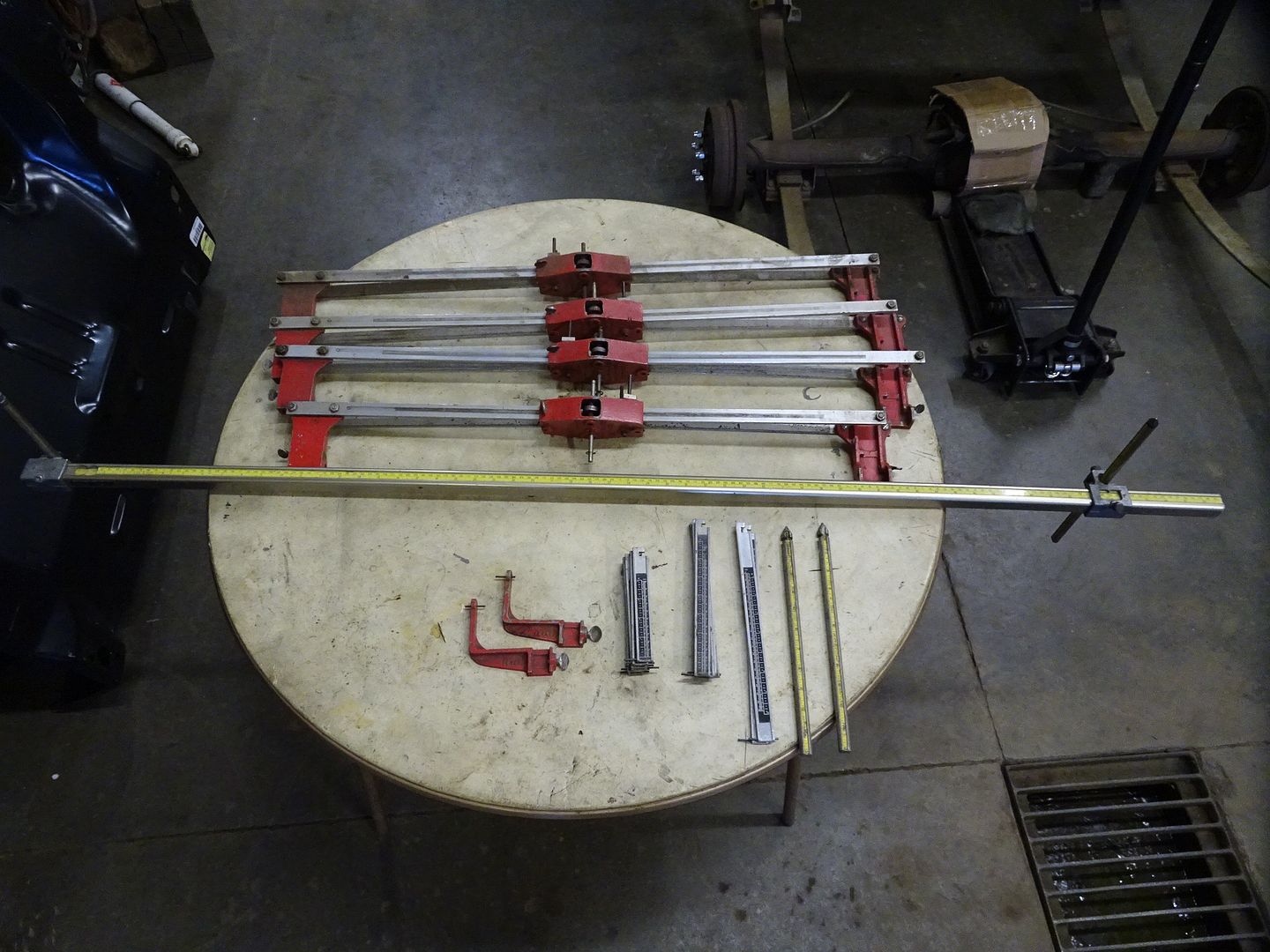
This poor car had been smacked around multiple times and this was one of the "neat" bondo repairs it had done to it.
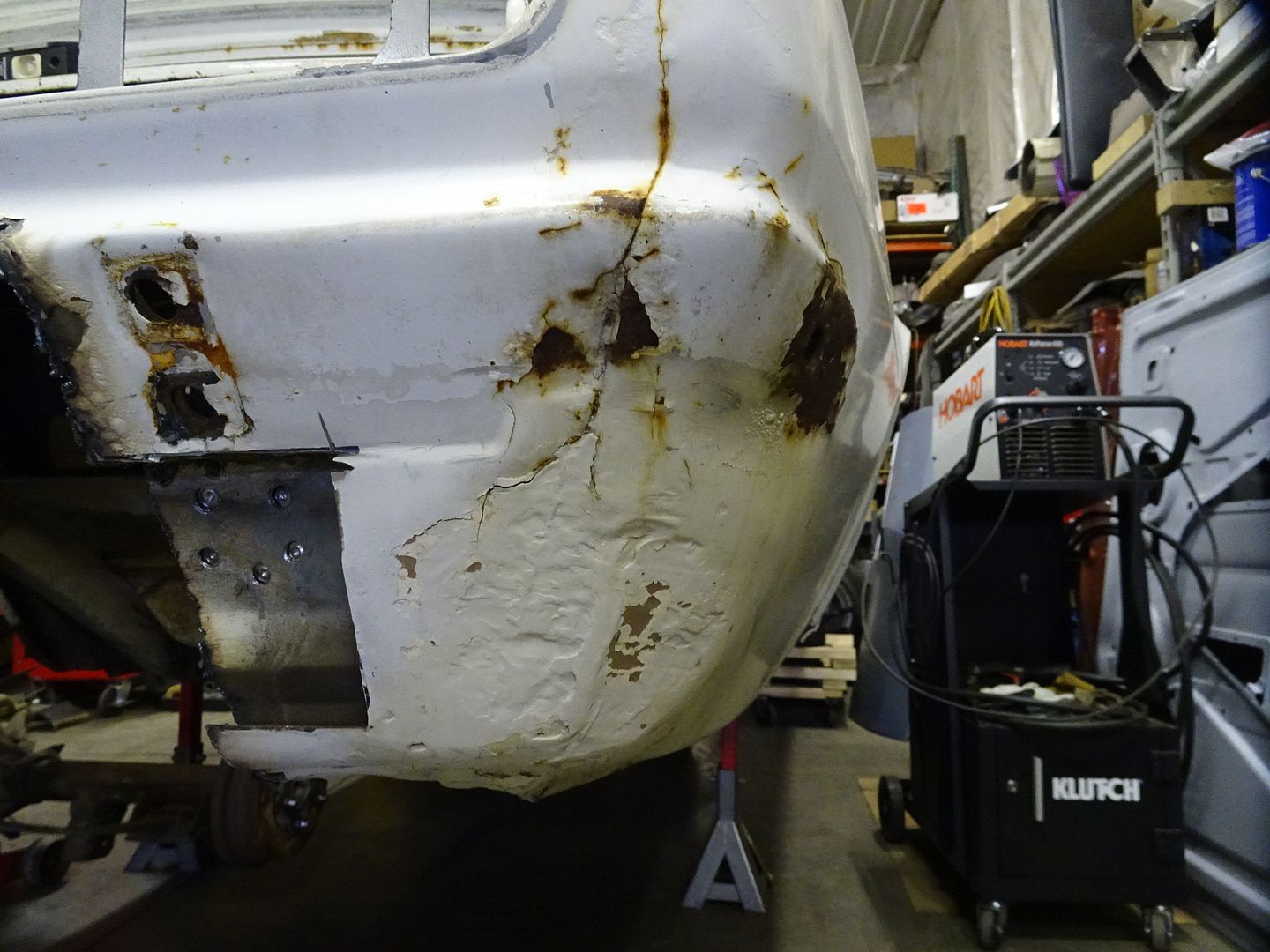
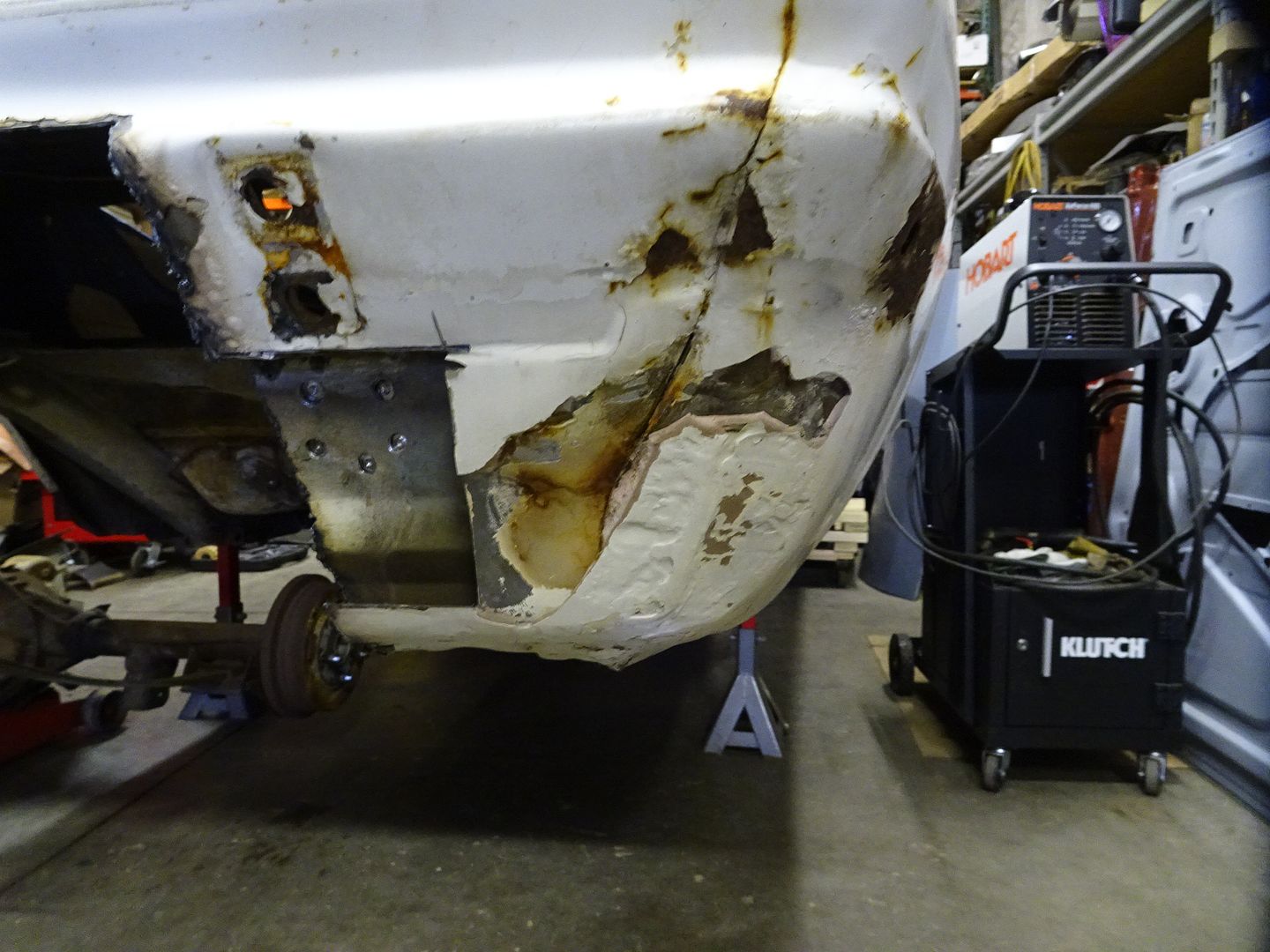
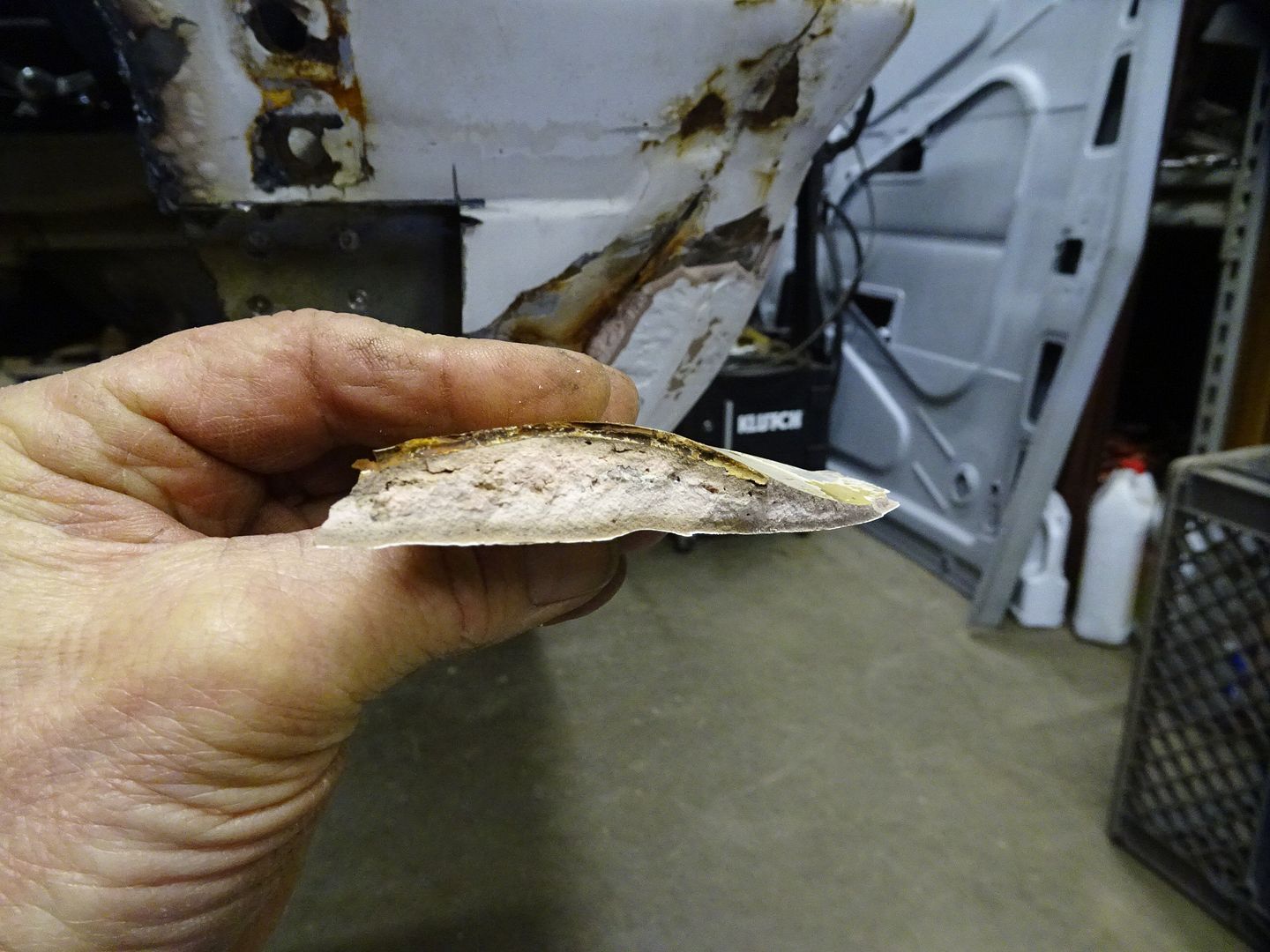
Long story, short version, I did many small repairs and "adjustments" along the way to replacing the floor as well as most of the left inner wheel house.
Prepped and pre-drilled to weld to the frame rails and drops.
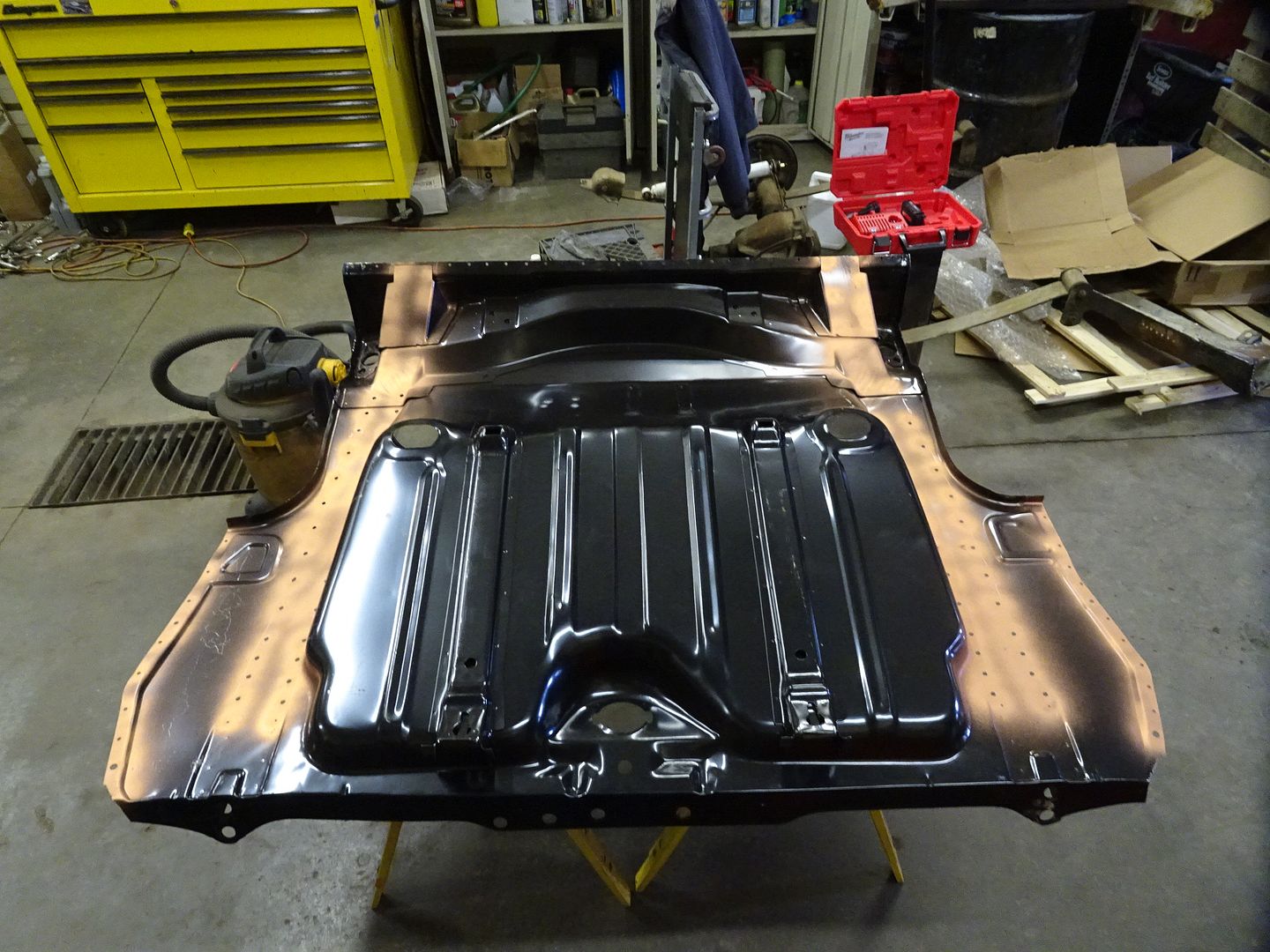
Fitting the wheel house.
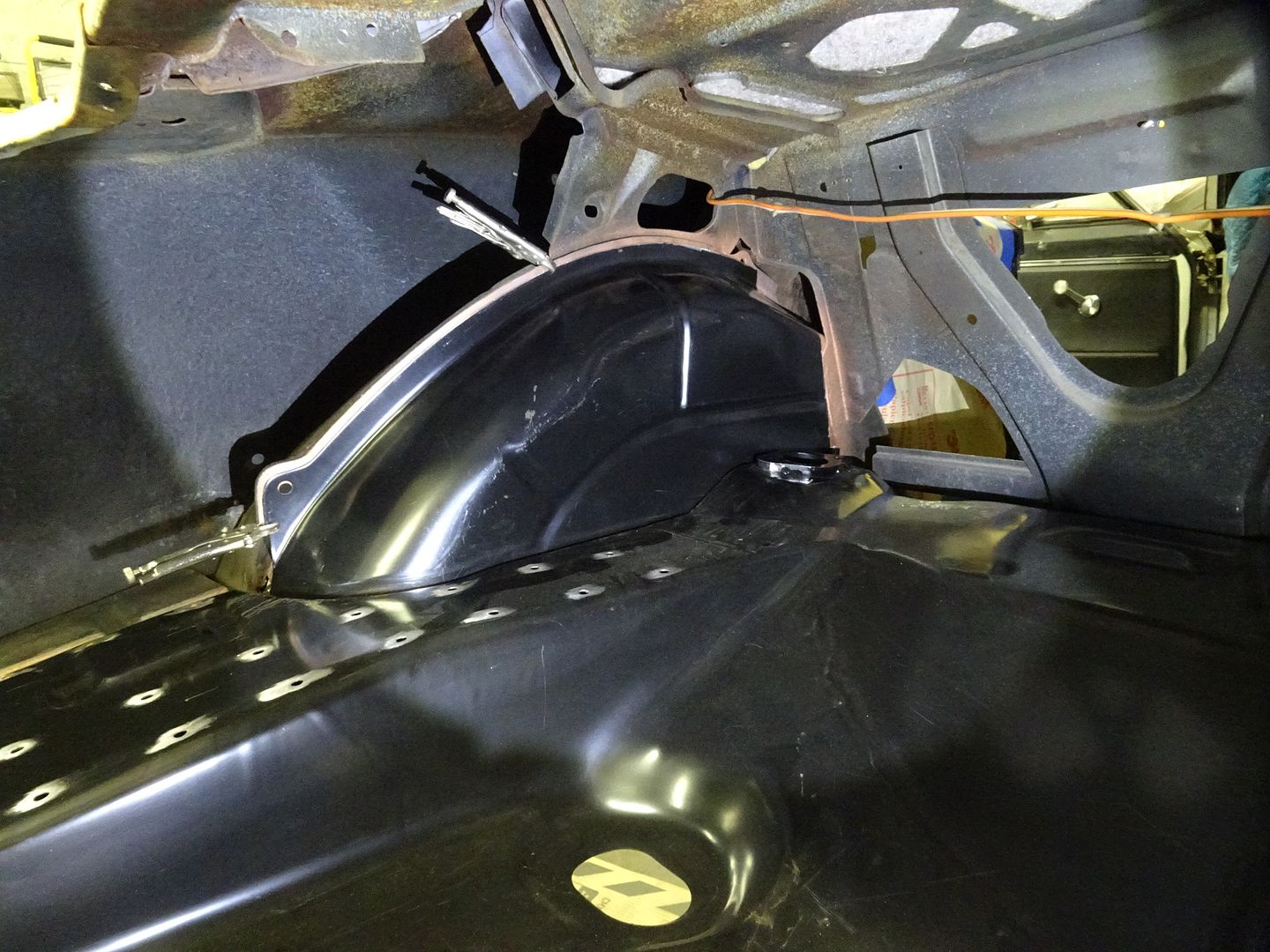
All measured, aligned, clamped and ready to weld
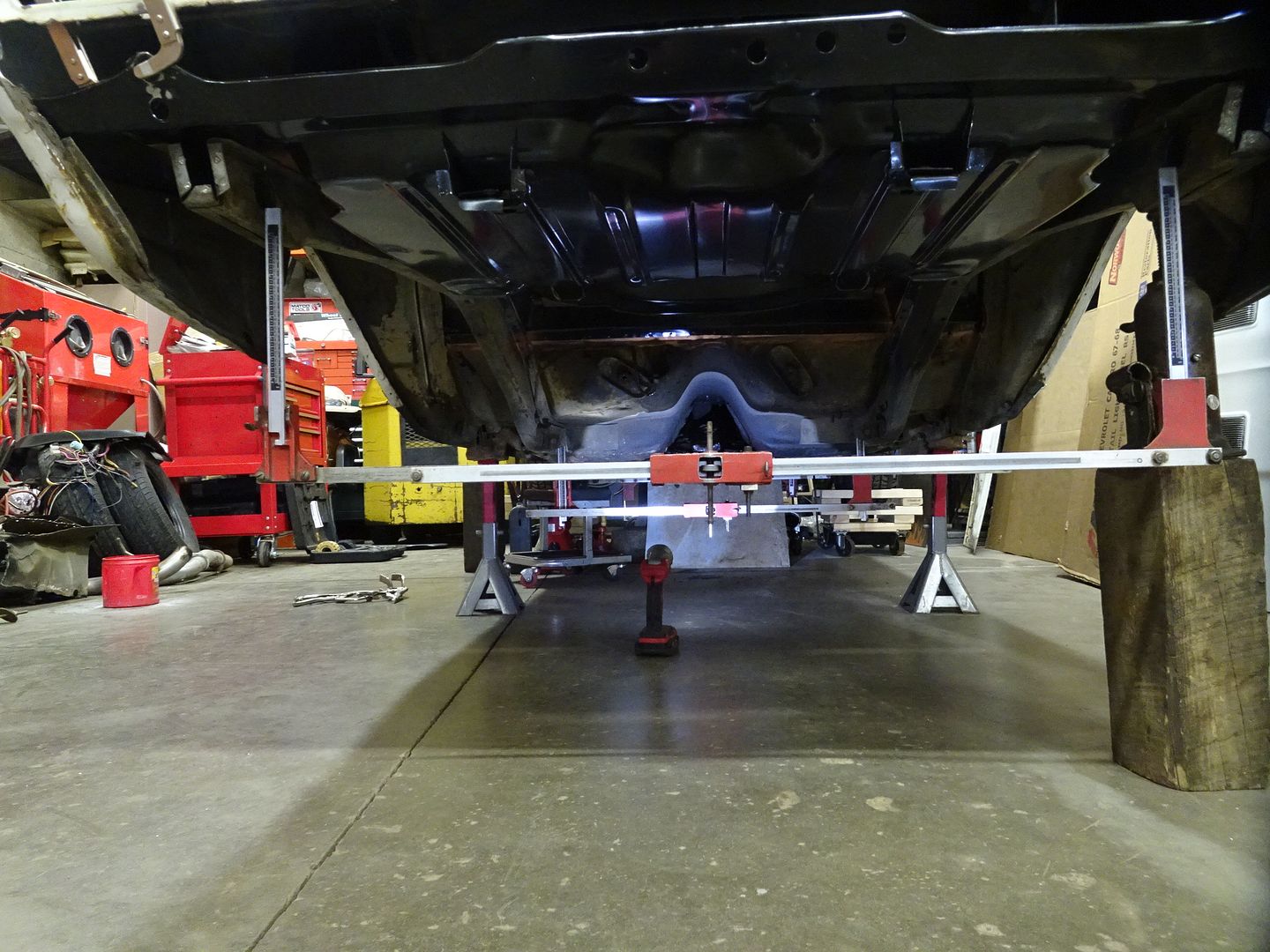
And the welding fun begins.
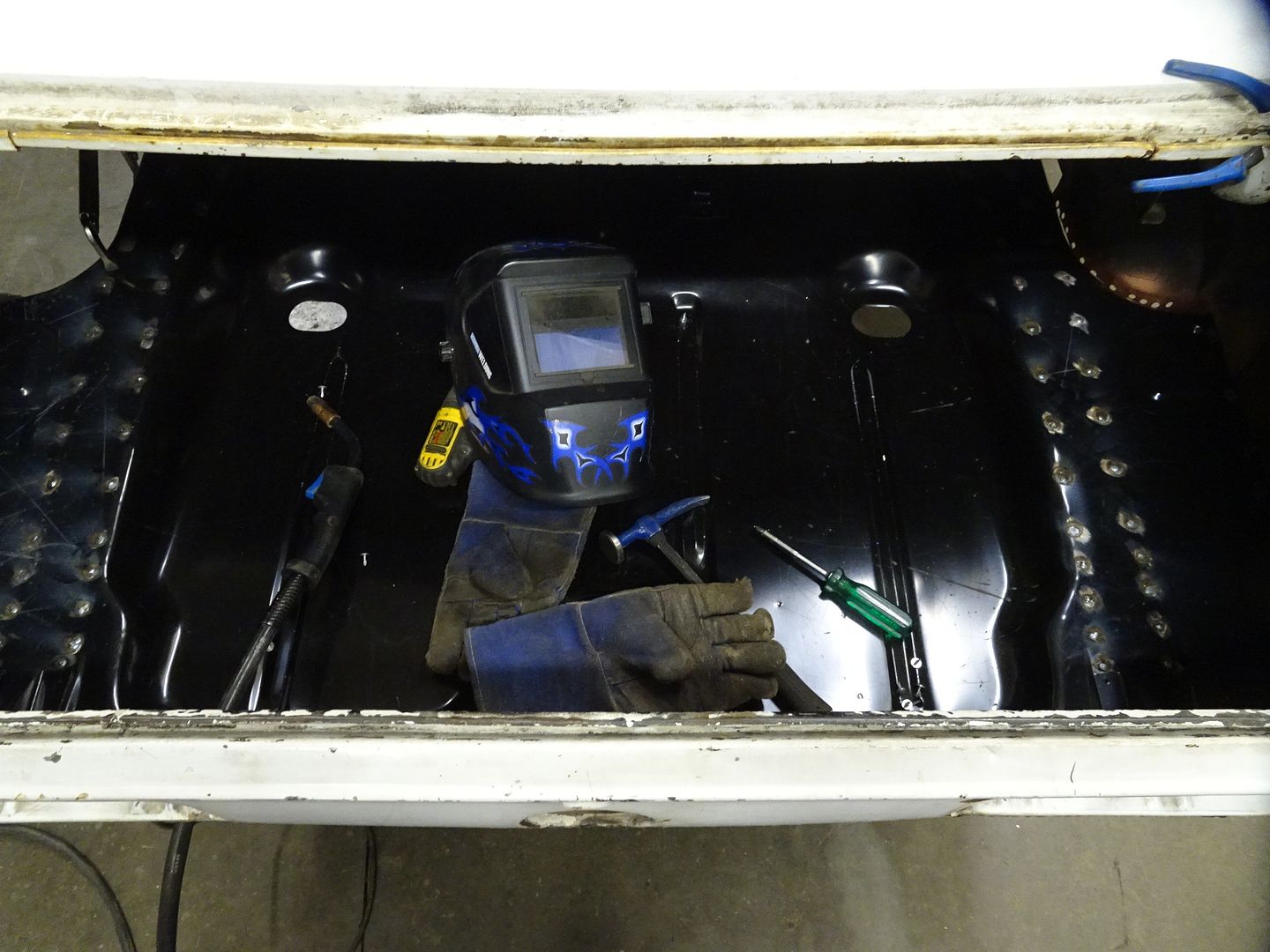
My shop driveway March 9 2019. We got 2" of rain and that is 300 ft of ice slide to the road. The culvert was frozen and the ditch flooded and overran the driveway, washing out the gravel. What a fun 2 days that was cleaning up that mess... anyway, back to the program.
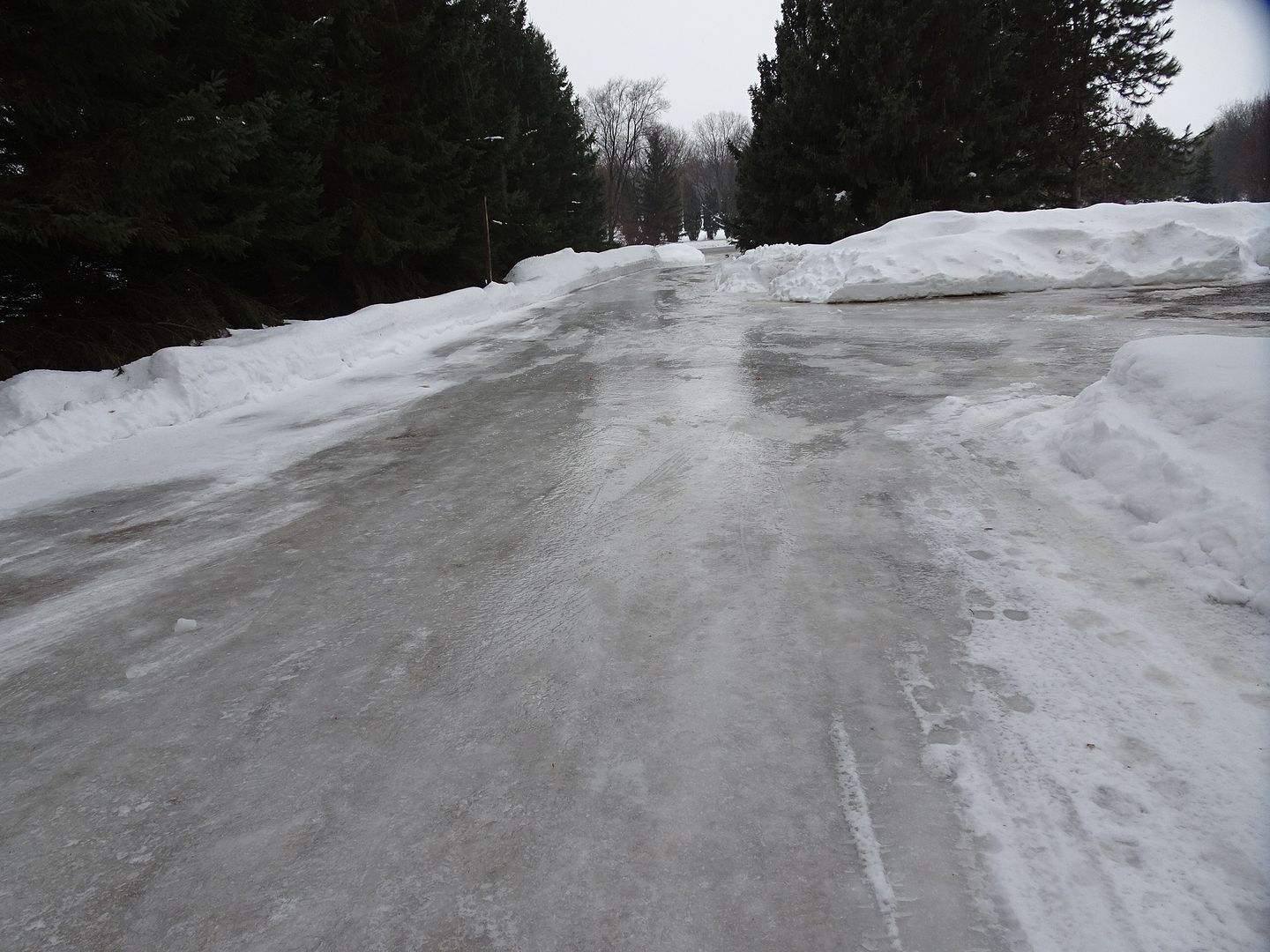
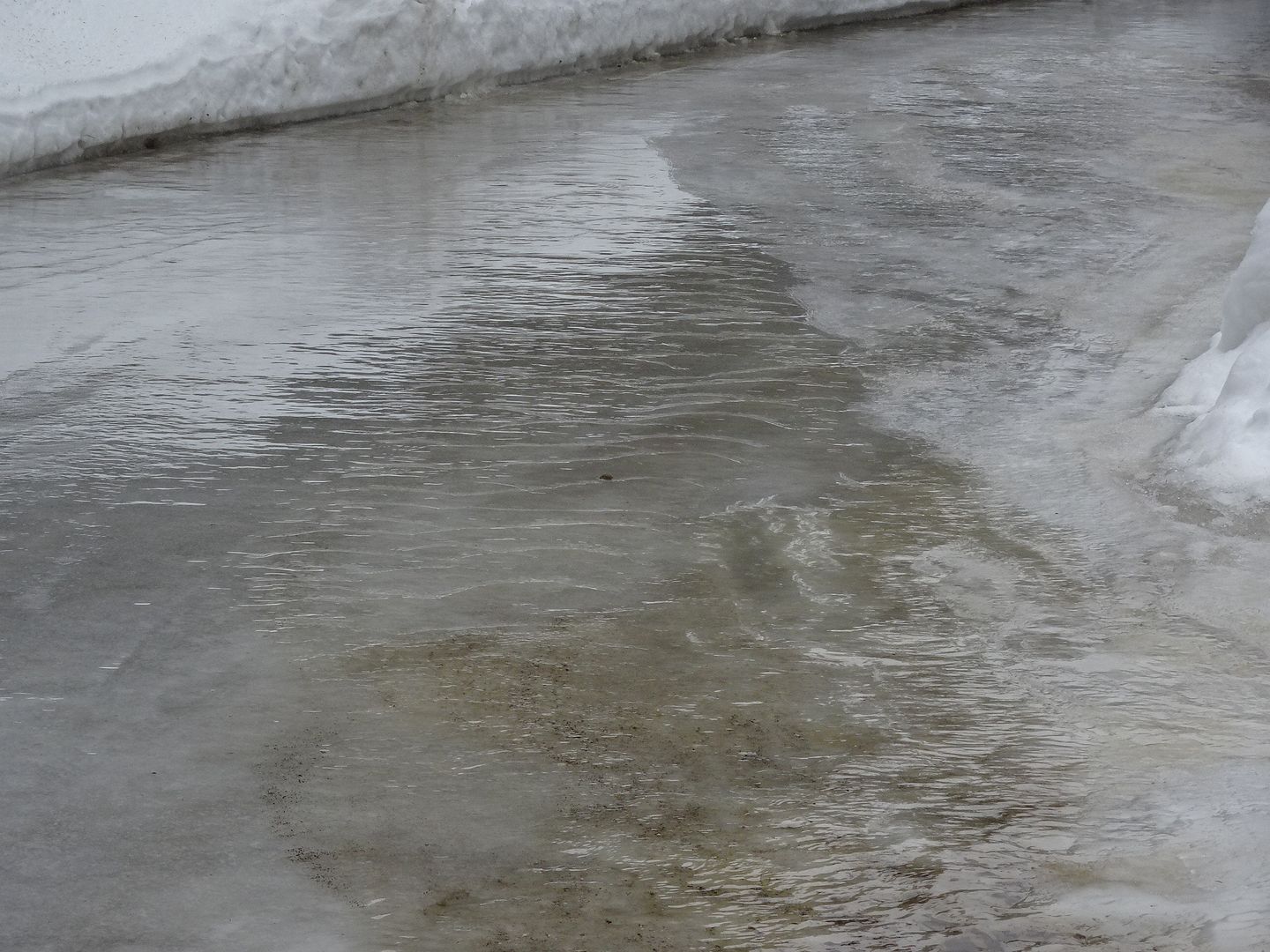