Dean Jenkins
Promoted Users
First, I talked with Barry and made sure this post was OK. Not only did he say it was OK, he enthusiastically encouraged me to pursue this. What a great guy!
In addition to being a car restoration enthusiast and amateur painter, I am an entrepreneur. I've started two businesses. One failed, one is thriving. I've learned a lot, the hard way, and I know what it takes to succeed.
I've been following several threads about sanding blocks. I've seen a lot of discussion about the benefits of using acrylic blocks to get panels really flat.
I also see many comments that "It is not the tool, it is the hand using the tool." Those are fair and accurate comments.
But, I think we can all agree, even if you can get great results without newer tools, having great tools makes things easier. (I've heard some guys just use a stir stick with sandpaper wrapped around it - and get show quality finishes, but c'mon!)
**Barry cracked me up. Even though he enthusiastically supported this idea, he confessed that he only uses a 4" X 6" "jitterbug" sander and the 4" rubber blocks from the '70's with the flaps and nails to hold the paper in place. And he gets great results because these tools are in an experienced hand. When I get these "Best Acrylic Sanding Blocks Ever" developed, I'm going to send him a set and challenge him to give them a try
Can you just cut some blocks, of varying thickness's, from acrylic, wrap paper around them, and go to town? Sure. But the ergonomics are bad. They are hard to hold onto and to control.
I want to create the "Best Acrylic Sanding Blocks Ever"
I've looked very closely at all the Acrylic Sanding Blocks currently being offered.
Here are the top 3 most most visible suppliers:
Linear Blocking Tools
True Blox (I actually bought a set of these)
Big Kid Blocks
bkblocks.com
IMHO these products all have shortcomings and are ridiculously overpriced!
The biggest shortcoming are the ergonomics/shapes of the handles. Particularly TrueBlox and Big Kid Blocks. Linear Blocking has an innovative handle, but man, they are expensive, and the handle has "issues," notably they can pinch your hands on concave surfaces.
I've seen many comments that AFS blocks had awesome ergonomics. People loved them!
But, they were still foam blocks, albeit with steel tension rods, but did not have the acrylic base that seems to provide the ability for superior flattening.
So, I am going to develop the "Best Acrylic Sanding Blocks Ever" incorporating the ergonomics of AFS blocks with the advantages of an acrylic base.
Here are the stages of developing a product and then bringing it to market and the current status:
In the near future, I will be looking for;
Any thoughts and feedback are very welcome!
This should be fun . . .
In addition to being a car restoration enthusiast and amateur painter, I am an entrepreneur. I've started two businesses. One failed, one is thriving. I've learned a lot, the hard way, and I know what it takes to succeed.
I've been following several threads about sanding blocks. I've seen a lot of discussion about the benefits of using acrylic blocks to get panels really flat.
I also see many comments that "It is not the tool, it is the hand using the tool." Those are fair and accurate comments.
But, I think we can all agree, even if you can get great results without newer tools, having great tools makes things easier. (I've heard some guys just use a stir stick with sandpaper wrapped around it - and get show quality finishes, but c'mon!)
**Barry cracked me up. Even though he enthusiastically supported this idea, he confessed that he only uses a 4" X 6" "jitterbug" sander and the 4" rubber blocks from the '70's with the flaps and nails to hold the paper in place. And he gets great results because these tools are in an experienced hand. When I get these "Best Acrylic Sanding Blocks Ever" developed, I'm going to send him a set and challenge him to give them a try
Can you just cut some blocks, of varying thickness's, from acrylic, wrap paper around them, and go to town? Sure. But the ergonomics are bad. They are hard to hold onto and to control.
I want to create the "Best Acrylic Sanding Blocks Ever"
I've looked very closely at all the Acrylic Sanding Blocks currently being offered.
Here are the top 3 most most visible suppliers:
Linear Blocking Tools
True Blox (I actually bought a set of these)

True Blox
Helping you elevate your results in high end Body Work & Paint on hot rods and concours restorations.
www.trueblox.com
Big Kid Blocks
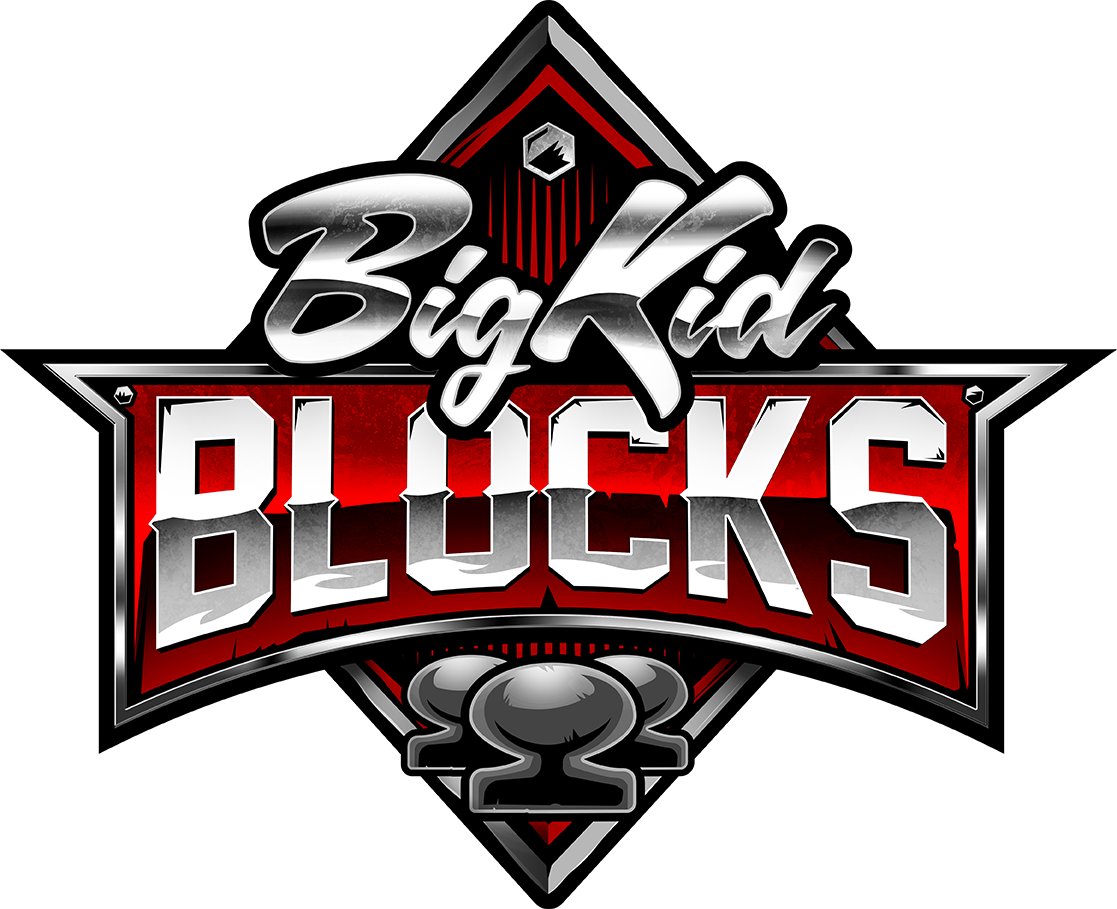
Big Kid Blocks
Your one-stop shop for custom sanding blocks, detail kits and body shop accessories!

IMHO these products all have shortcomings and are ridiculously overpriced!
The biggest shortcoming are the ergonomics/shapes of the handles. Particularly TrueBlox and Big Kid Blocks. Linear Blocking has an innovative handle, but man, they are expensive, and the handle has "issues," notably they can pinch your hands on concave surfaces.
I've seen many comments that AFS blocks had awesome ergonomics. People loved them!
But, they were still foam blocks, albeit with steel tension rods, but did not have the acrylic base that seems to provide the ability for superior flattening.
So, I am going to develop the "Best Acrylic Sanding Blocks Ever" incorporating the ergonomics of AFS blocks with the advantages of an acrylic base.
Here are the stages of developing a product and then bringing it to market and the current status:
- Concept and initial design sketches (This is done)
- 3D CAD files created (This is done - I will share them as soon as I have the patent application filed - got to protect the IP)
- 3D printing of prototype (This will be done within a few weeks)
- Creation of molds for injection molding (This is expected within about 2 months)
- Volume production (This is expected within about 3 months)
- Launch and ship product! (This is expected within 3-6 months)
In the near future, I will be looking for;
- Input on what real users of the product want in the "Best Acrylic Sanding Blocks Ever"
- Feedback on the 3D draft product images.
- Crowdfunding for the molds. This is the most expensive part of a product launch. I'm looking for early adopters to be a part of this launch. The current product offerings are priced at ~$150 for an entry set of blocks. I'm looking at a lower price point. Once the design is locked down, these can be produced (In the United States!) for pretty cheap. For the "Crowdfunding," I'm anticipating about a $50 "GoFundMe" contribution campaign that will get you in on the design of the product and a set of six blocks from the first production run. If I can get 50-100 people in on this, the molds will be funded.
Any thoughts and feedback are very welcome!
This should be fun . . .