Seems awhile back I stumbled on a post addressing this problem, o/c now that I need it it's MIA.
.035 material, 28 amps using tig, tacked about every 3/8" or so. I think 28 was a little too hot, judging how flat the welds were.
Wrapped the ends first with two short "U" shaped passes, then 3 or 4 short stitches on each run down the sides.
All tacked in, everything was nice and flush.
After welding, entire patch was about 5 to 10 thou low from the end surfaces.
Couldn't planish tacks or weld like I'd liked to given the "C" channel shape on the backside.
Sorry didn't get any shots immediately after welding...too anxious to fix the issue.
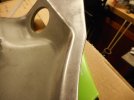
Able to get it hammered back out and finished ok I guess, just wondering if this is normal or do I need to change my recipe and/or tack something like this in a little proud next time to compensate.
I'm thinking the angled sides had something to do with this problem.
Got another patch to do just like this in the next few days and hoping to counter it.
.035 material, 28 amps using tig, tacked about every 3/8" or so. I think 28 was a little too hot, judging how flat the welds were.
Wrapped the ends first with two short "U" shaped passes, then 3 or 4 short stitches on each run down the sides.
All tacked in, everything was nice and flush.
After welding, entire patch was about 5 to 10 thou low from the end surfaces.
Couldn't planish tacks or weld like I'd liked to given the "C" channel shape on the backside.
Sorry didn't get any shots immediately after welding...too anxious to fix the issue.
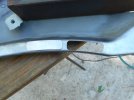
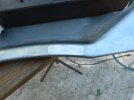
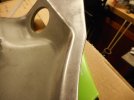
Able to get it hammered back out and finished ok I guess, just wondering if this is normal or do I need to change my recipe and/or tack something like this in a little proud next time to compensate.
I'm thinking the angled sides had something to do with this problem.
Got another patch to do just like this in the next few days and hoping to counter it.