Looking for some advice. The '70 Datsun 200 I'm working on has had 1 1/4 panel either replaced or repaired to where they took out the lead and filled with filler. The other side had the, I'm assuming, original lead still in it. I don't have experience with lead and I'm looking for advice on whether I should start learning or go a different route, perhaps a fiberglass reinforced filler? Here are some pics of what I'm dealing with.
Bad side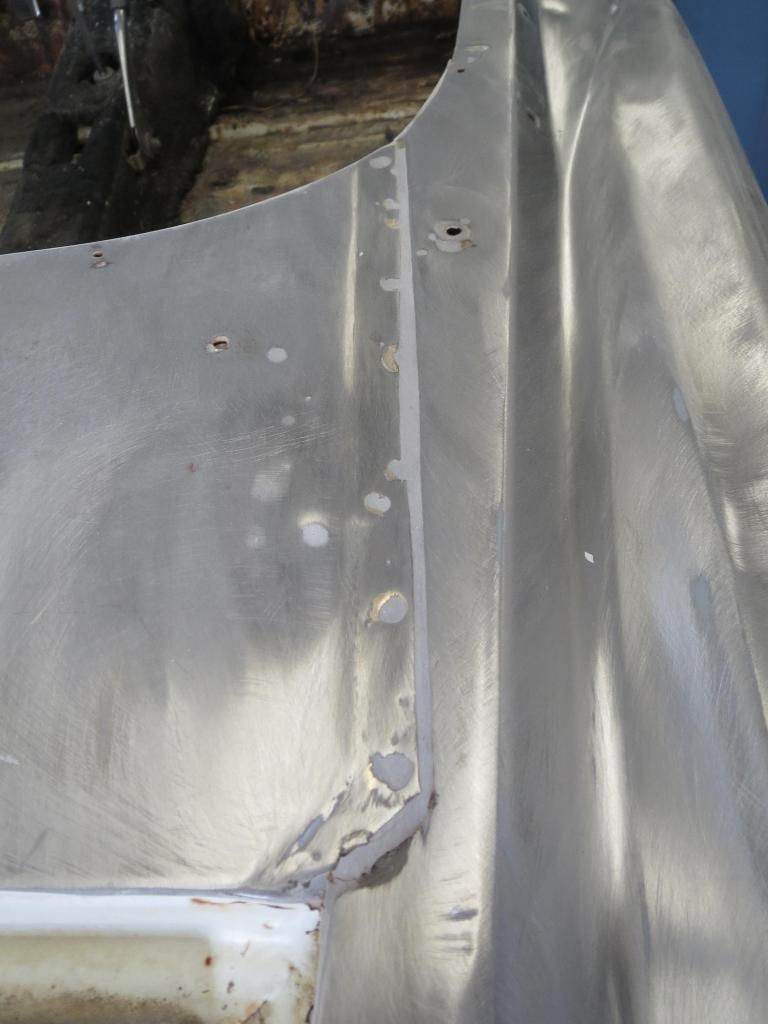
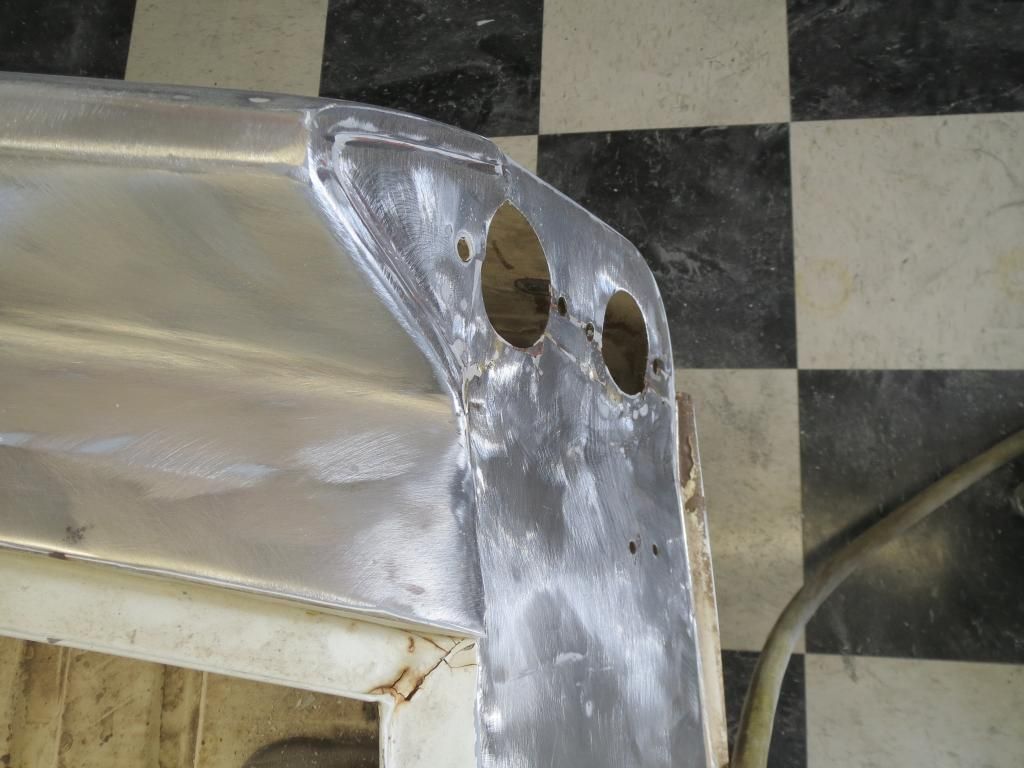
Good Side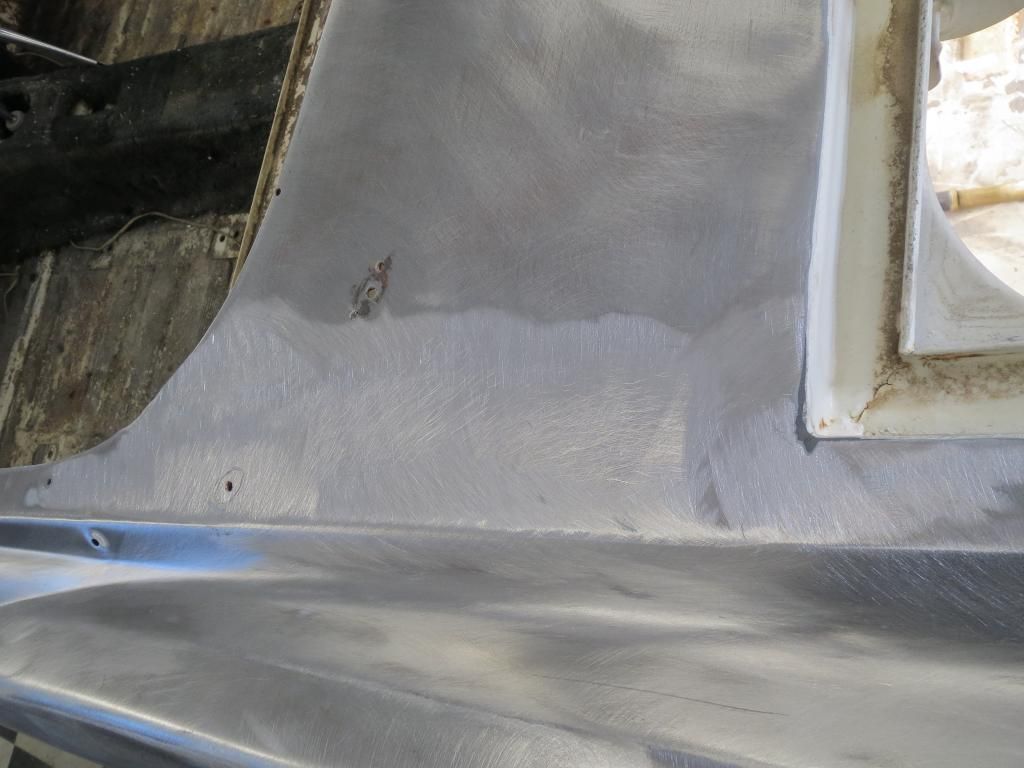
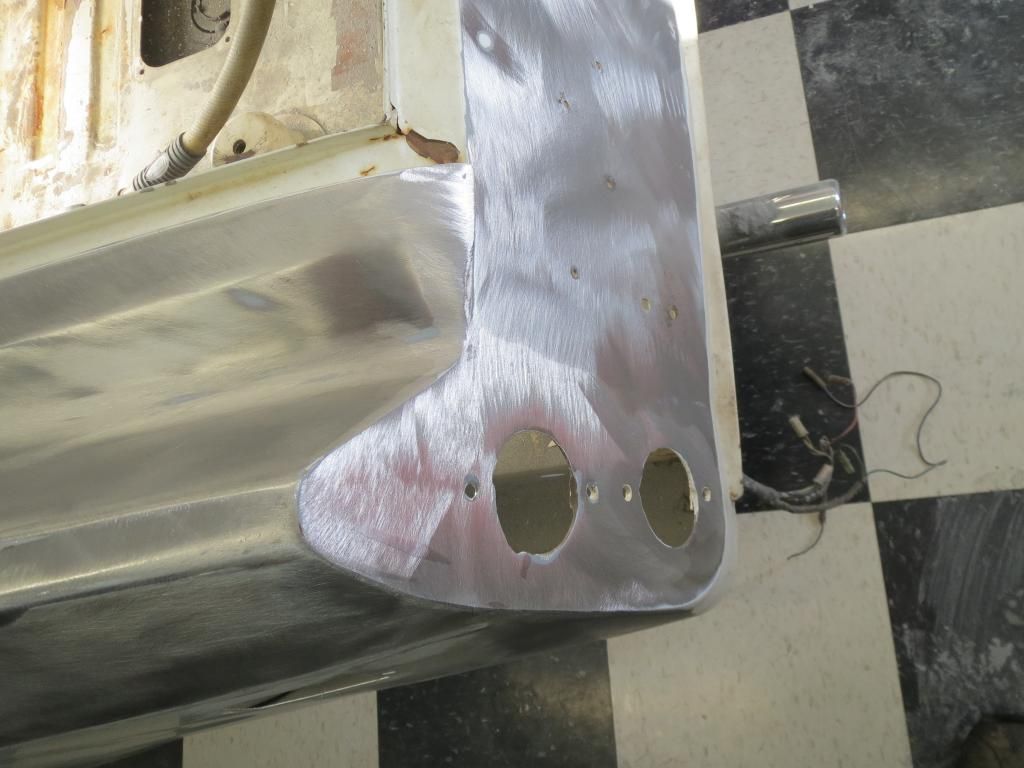
Bad side
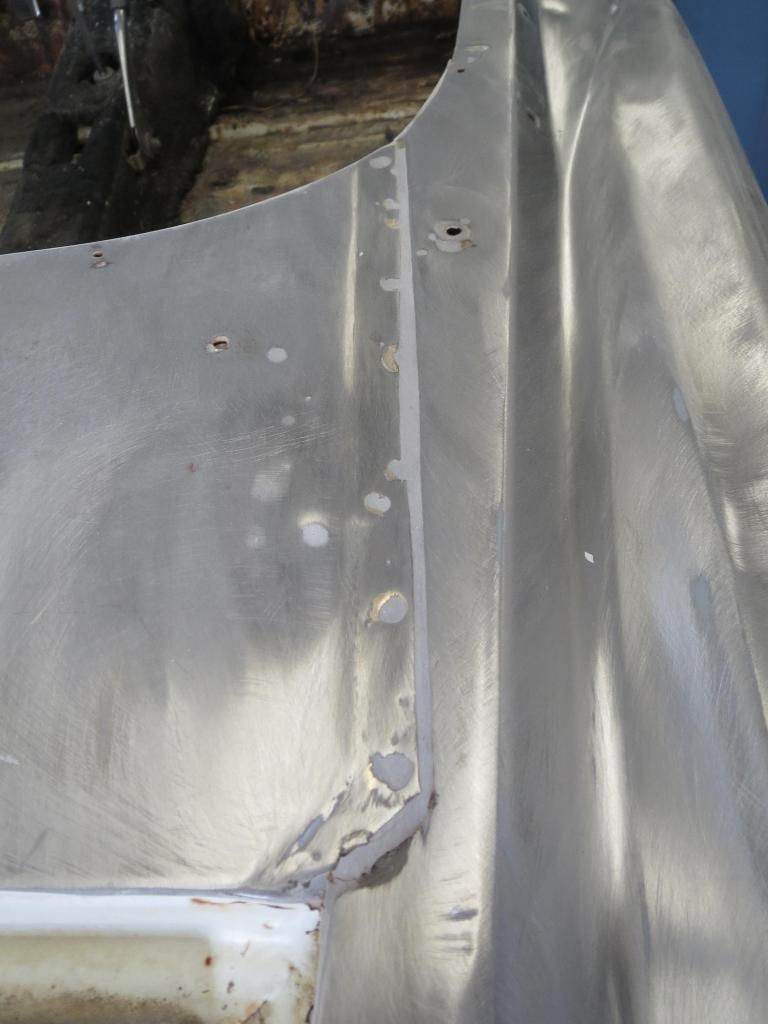
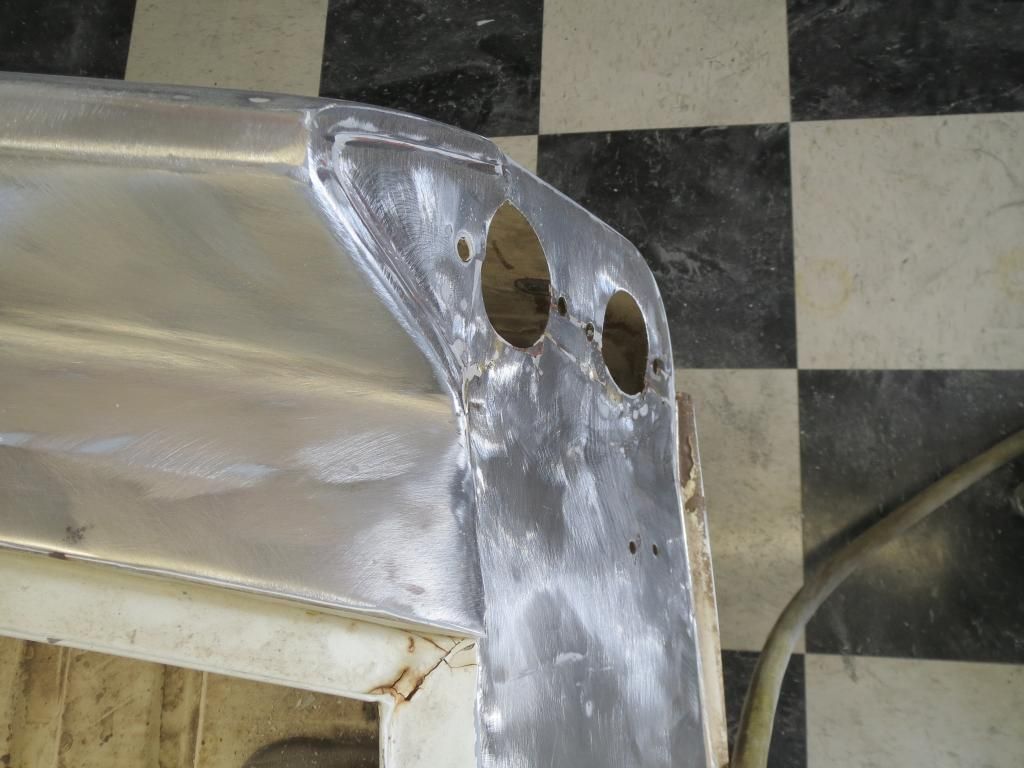
Good Side
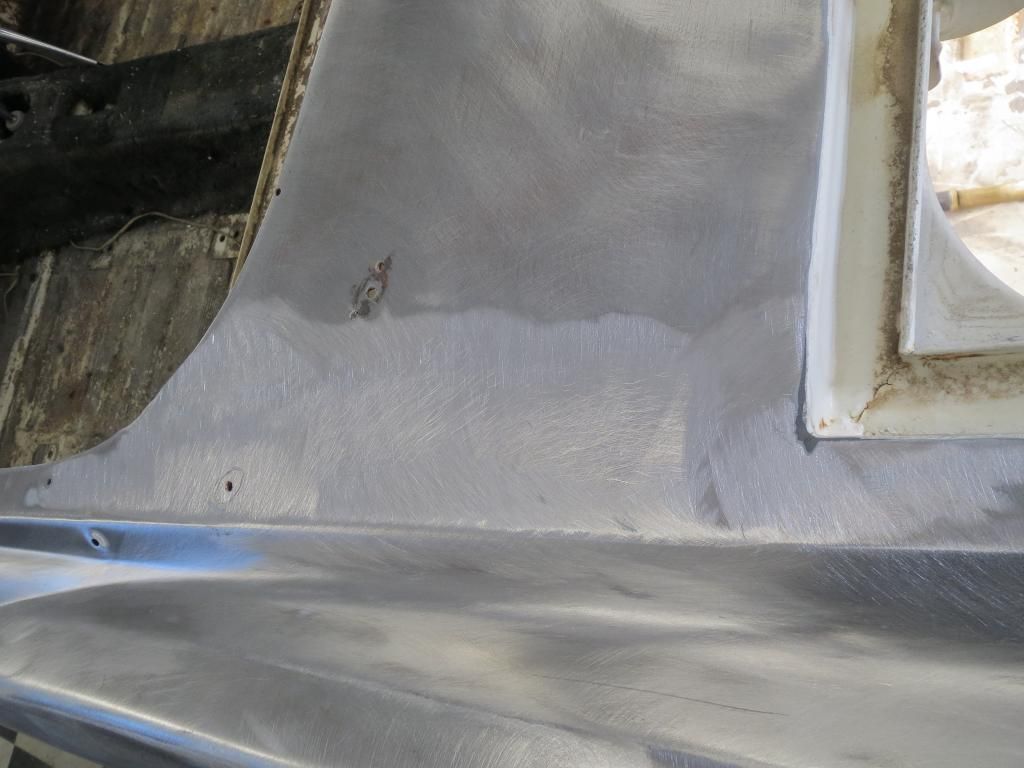
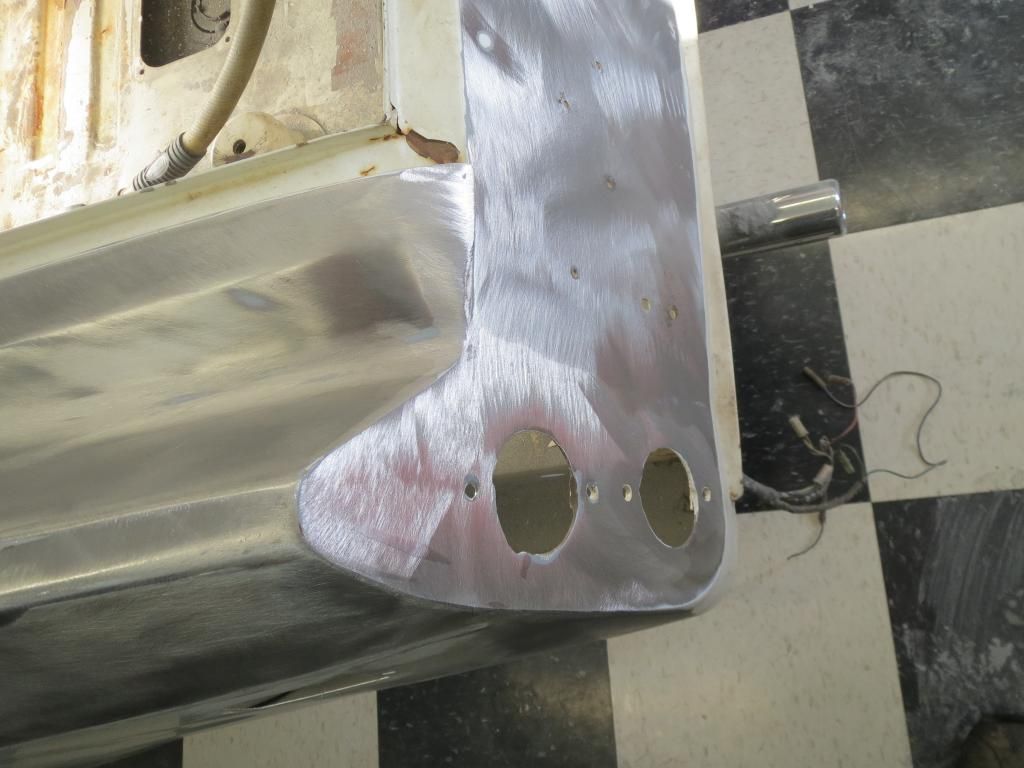