C
cstrom72
I had another post on my sunken weld woe's now since I couldnt massage it back out to proud the weld, i have some small "voids" on the edges of welds that I cannot grind out in fear of thinning the metal around it. What options do I have (see pic) I know I could spend the next week welding each little hole and grinding which I still think in turn is going to cause me more grief from excess grinding.
One place I read said to use TSP or CLR to clean the areas and or neutralize any oxidation then clean with the SPIs waterborn W&G remover then prime. Somewhere or someone also said if I get a spot sand blaster I can shoot the areas and that will remove the unwanted stuff in the small holes. Reccomendations???? thanks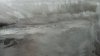
One place I read said to use TSP or CLR to clean the areas and or neutralize any oxidation then clean with the SPIs waterborn W&G remover then prime. Somewhere or someone also said if I get a spot sand blaster I can shoot the areas and that will remove the unwanted stuff in the small holes. Reccomendations???? thanks
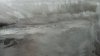