Thought I might post some of the work I've been doing on this mustang, I was hoping to paint it this summer, but as usual its taking longer than I thought to get it ready. I've had it tucked away for about 20 years, and finally got the urge to do something with it. I have several project cars and just do metal work on some of them, then sell them, and on some others I just rotate working on them. Metal work is what I like most, and I'm retired, so I work on what ever I feel like. This is what I started with on the mustang, and it looks like it just needs sanding and paint, but there was a lot of filler under that paint, not much rust, just bumps and bruises. There was rust in the quarters due to the factory trying to seal water out with foam, but it actually sealed water in, so I replaced them with NOS quarters. And the cowl was rusty due to leaves coming in the fresh air grill, cowl repair can be found here
http://www.spiuserforum.com/index.php?threads/fresh-air-system.8379/
I posted a thread about Door Alignment Pins awhile back, here is the link.
http://www.spiuserforum.com/index.php?threads/door-alignment-pins.9353/
Remounting fenders on the car is not as difficult as doors, but they still have their own problems, so I want a way to remove and reinstall them with ease. Unibody Mustangs have 6 mounting bolts along the top, and for repeatable alignment I concentrated on the very front and rear bolts. After getting it all aligned, the u-nuts were removed from those two bolt positions.

This is the rear bolt position with the u-nut removed. The red part is the inner fender/cowl connector.
My thought was to make the bolt hole in the fender just big enough for the bolt to pass through, but not allow any movement, which is 5/16 for 5/16 bolt. An extra parts fender provided the metal needed. Panel bond adhesive will be used to glue it to the bottom of the fender, and it will also take up the space left after removing the u-nut.
All thats needed now is a nut that won't move.
Welding a nut on the bottom side could be done, but I think adhesive will be easier and can be removed easily if needed by heating, so a piece of flat metal thick enough to be threaded was used.
The spacer and nut plate were both glued on while the fender was aligned where I wanted it.
I bought hood hinges for another 66 mustang 20 years ago, and the fit was even less than usuable, so I threw them away.
But the new ones they have available now fit and work excellent. Thank you Kentucky Mustang, they work like custom hinges.
http://www.spiuserforum.com/index.php?threads/fresh-air-system.8379/
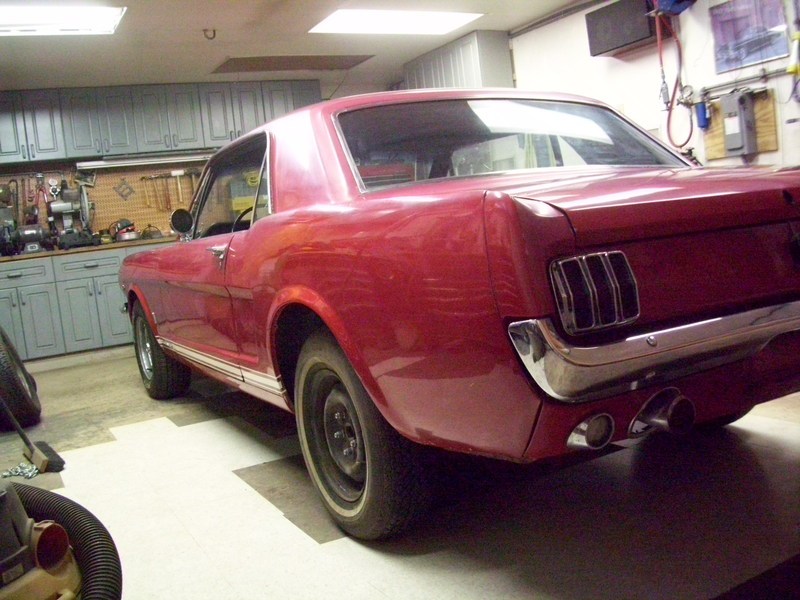
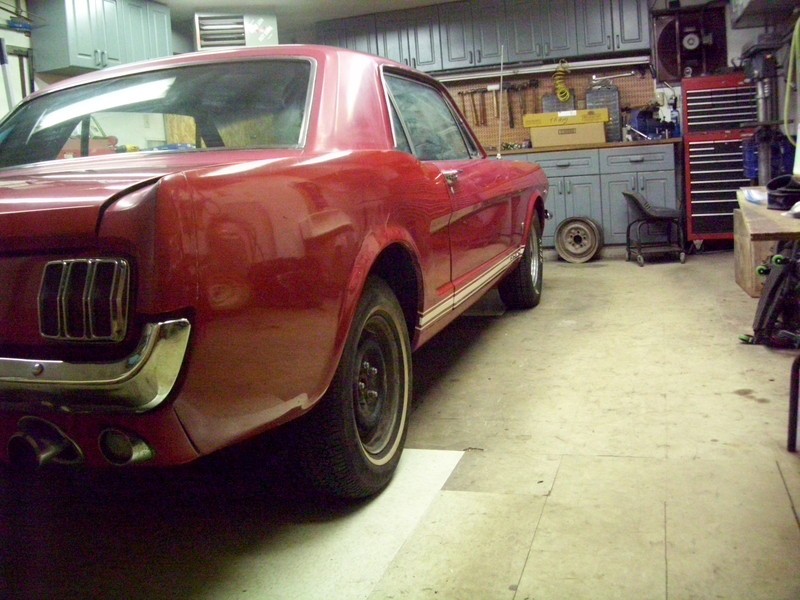
I posted a thread about Door Alignment Pins awhile back, here is the link.
http://www.spiuserforum.com/index.php?threads/door-alignment-pins.9353/
Remounting fenders on the car is not as difficult as doors, but they still have their own problems, so I want a way to remove and reinstall them with ease. Unibody Mustangs have 6 mounting bolts along the top, and for repeatable alignment I concentrated on the very front and rear bolts. After getting it all aligned, the u-nuts were removed from those two bolt positions.
This is the rear bolt position with the u-nut removed. The red part is the inner fender/cowl connector.
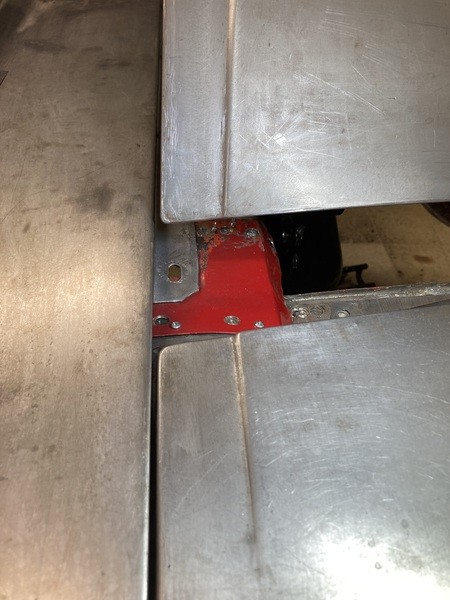
My thought was to make the bolt hole in the fender just big enough for the bolt to pass through, but not allow any movement, which is 5/16 for 5/16 bolt. An extra parts fender provided the metal needed. Panel bond adhesive will be used to glue it to the bottom of the fender, and it will also take up the space left after removing the u-nut.
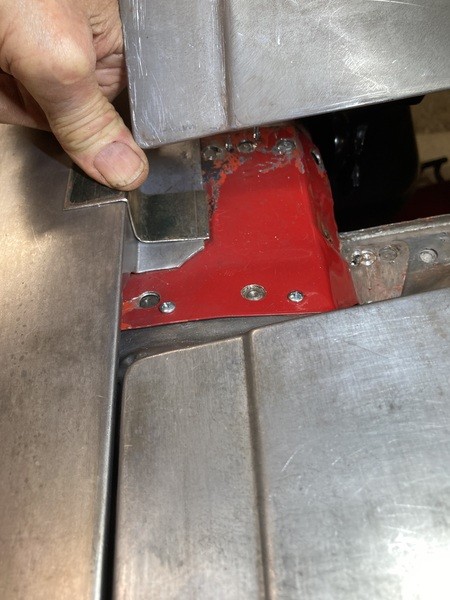
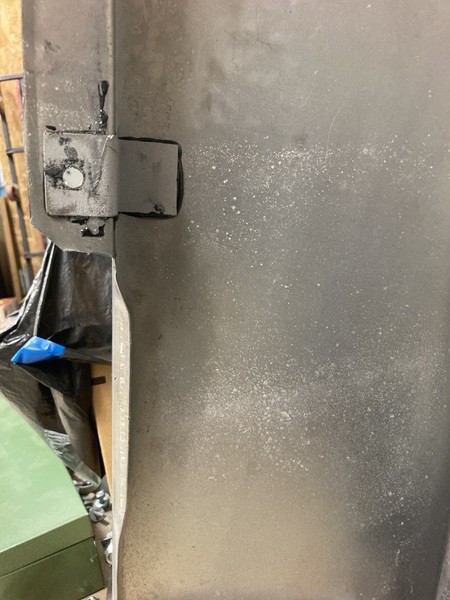
All thats needed now is a nut that won't move.
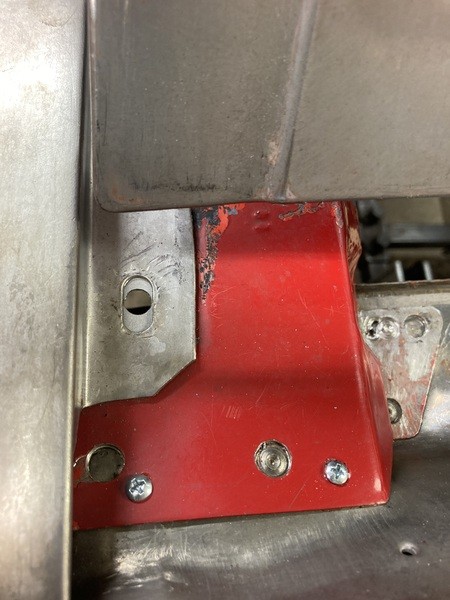
Welding a nut on the bottom side could be done, but I think adhesive will be easier and can be removed easily if needed by heating, so a piece of flat metal thick enough to be threaded was used.
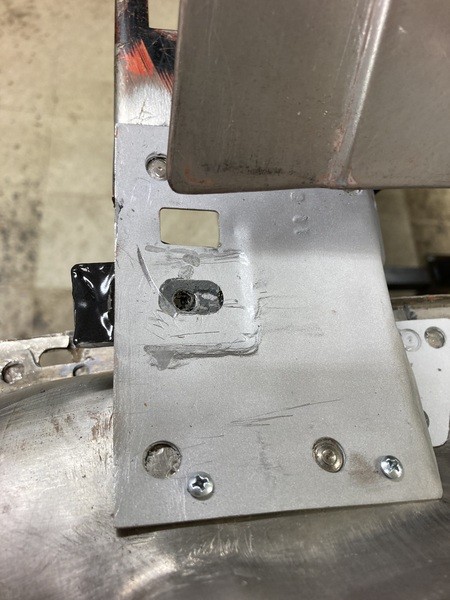
The spacer and nut plate were both glued on while the fender was aligned where I wanted it.
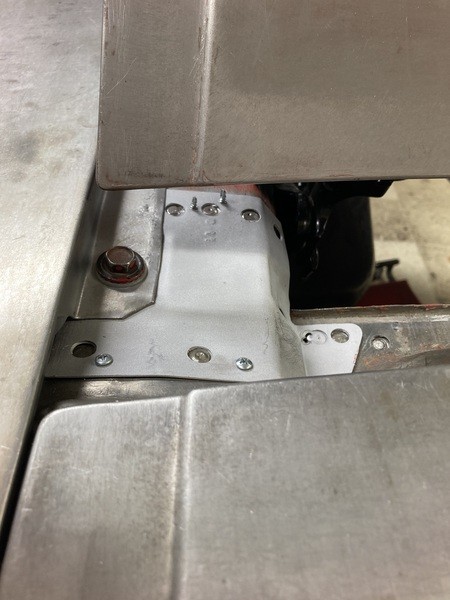
I bought hood hinges for another 66 mustang 20 years ago, and the fit was even less than usuable, so I threw them away.
But the new ones they have available now fit and work excellent. Thank you Kentucky Mustang, they work like custom hinges.
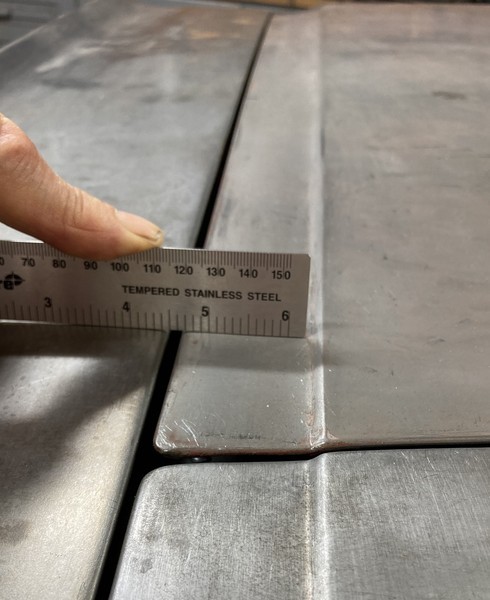
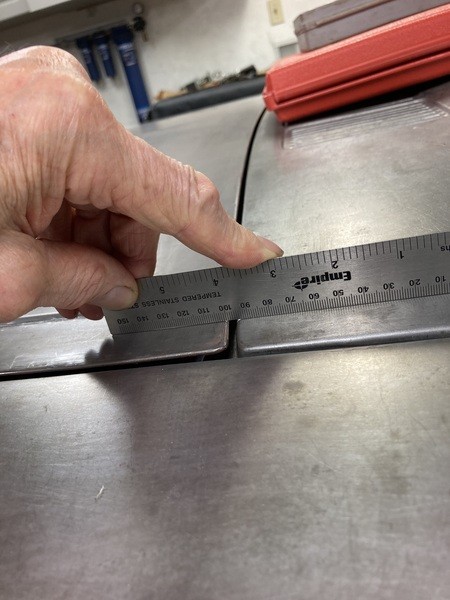