rusty428cj
Rusty Gillis
This is what we are starting with. There is not a lot of rust but since Ford did not prime a lot of the inner structure we will be removing all the sheetmetal do any needed rust repair and epoxy priming. The plans are to install Rod & Custom front and rear suspension, Wilwood brakes, Currie 9", AOD and a 347. The body mods will be fender flares, drip rails removed, cowl vents filled in and maybe a few other things as we go.
One of the first things we did after bracing the body was to remove the cowl
The quarter panels were removed
The roof was also removed and there was only surface rust but in a few years it will get worse if it is not cleaned up now
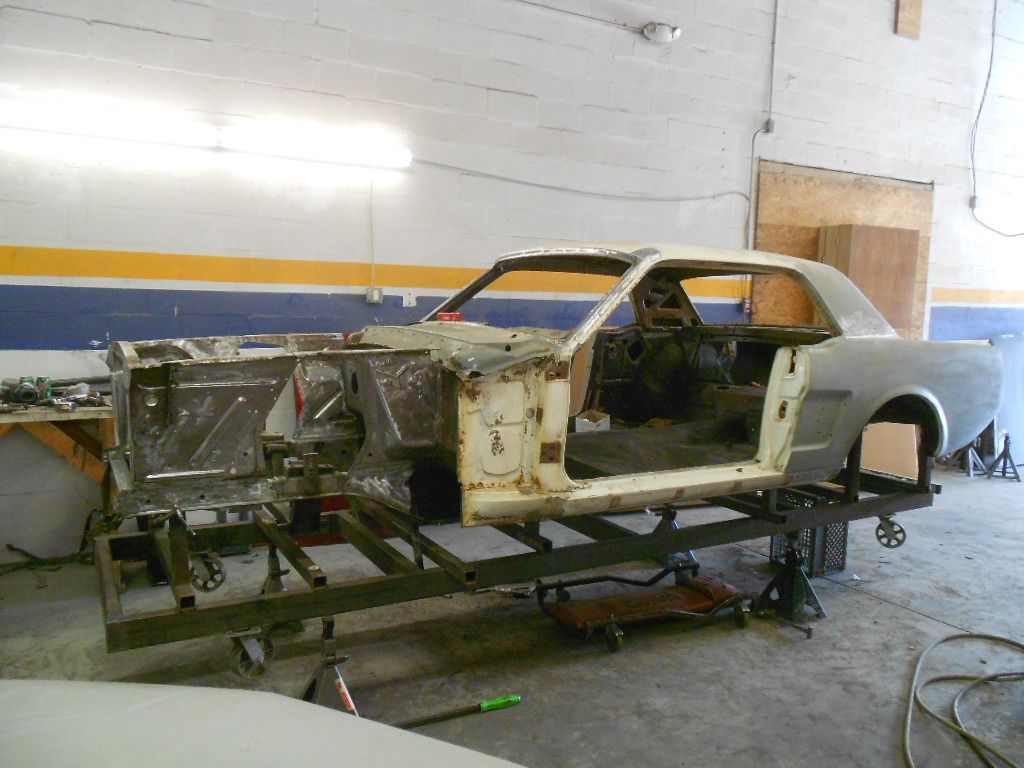
One of the first things we did after bracing the body was to remove the cowl
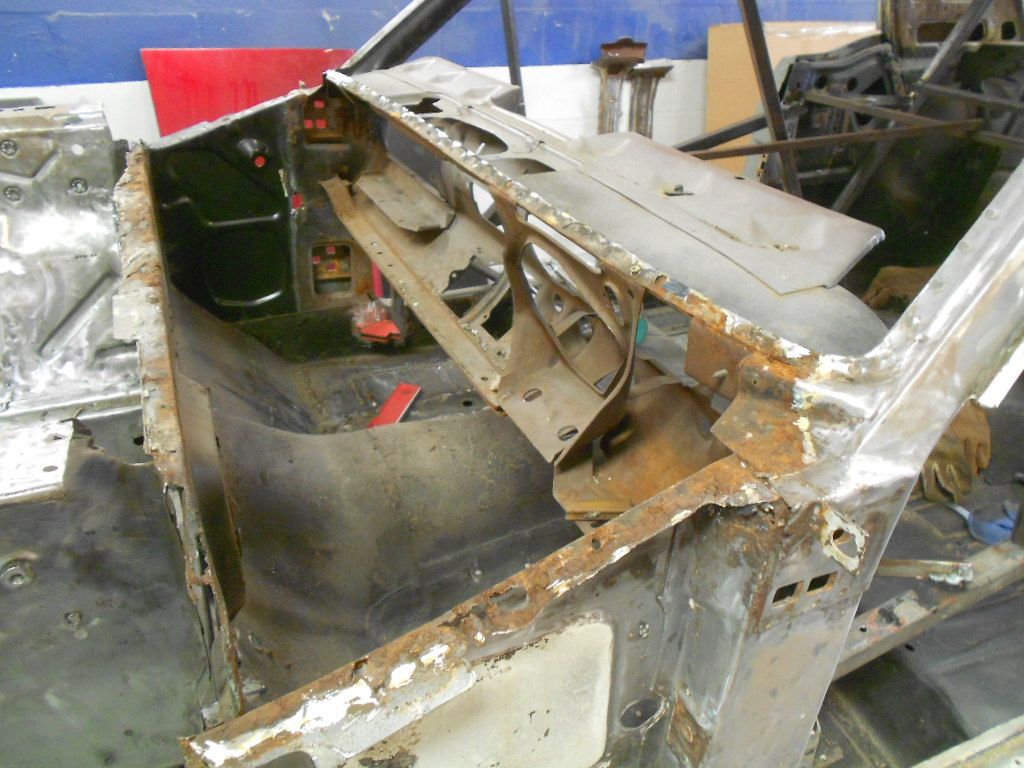
The quarter panels were removed
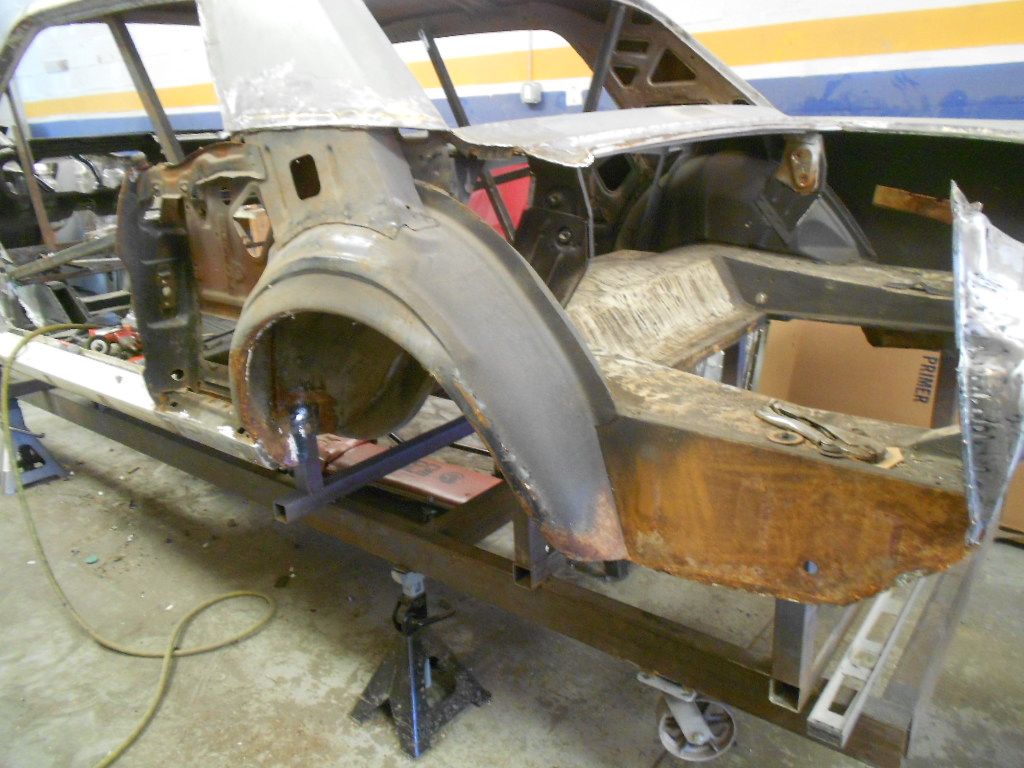
The roof was also removed and there was only surface rust but in a few years it will get worse if it is not cleaned up now
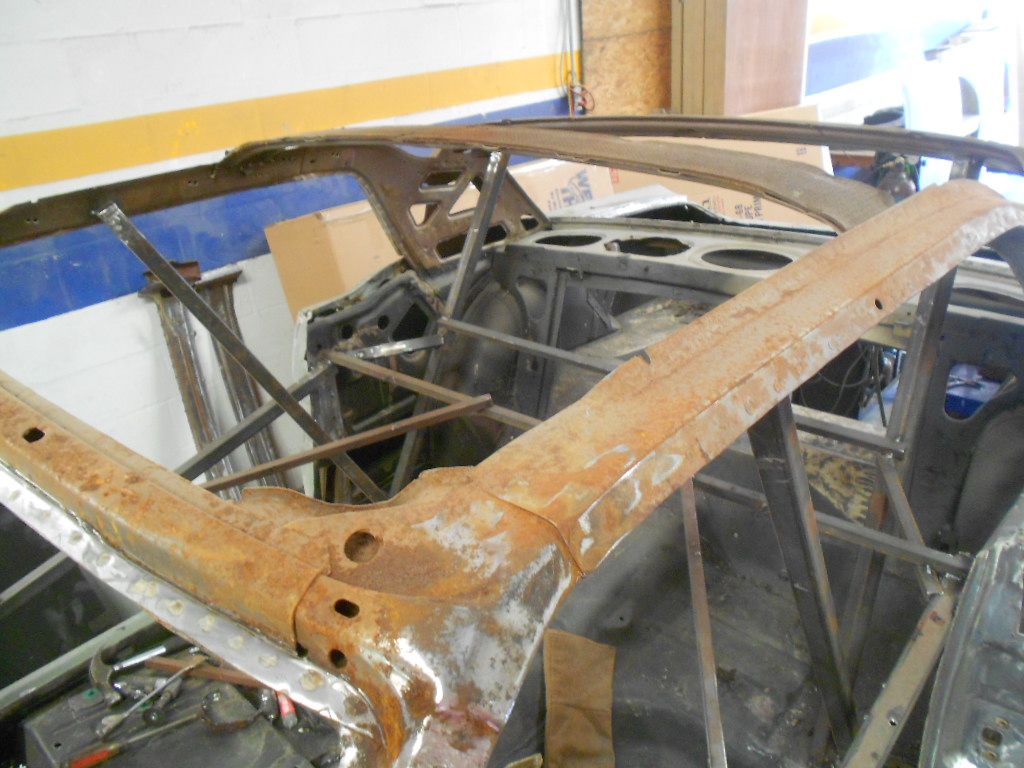