rusty428cj
Rusty Gillis
Brian started putting the puzzle back together
He tacked this in place and than decided he had had enough for one day and will finish on Monday.
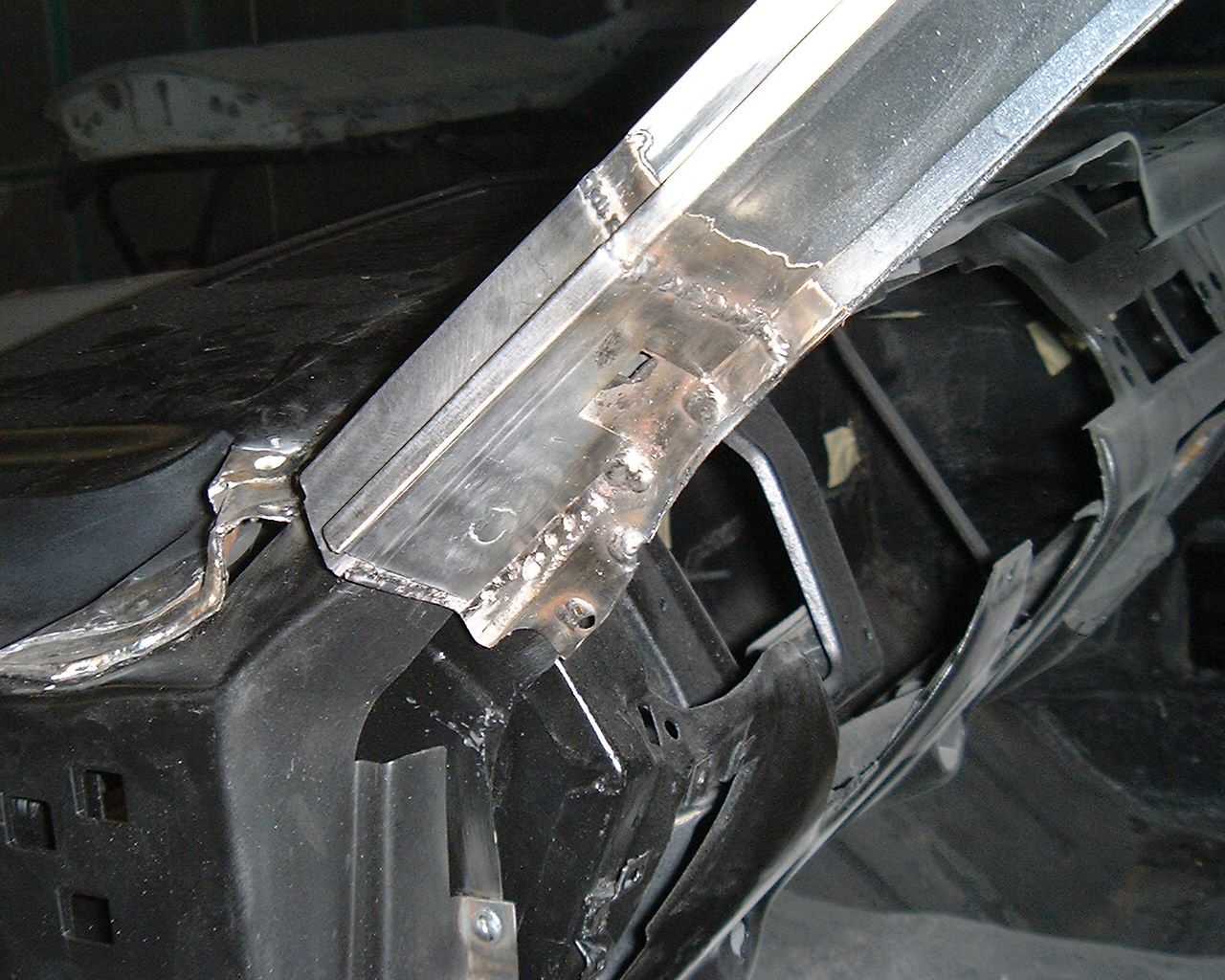
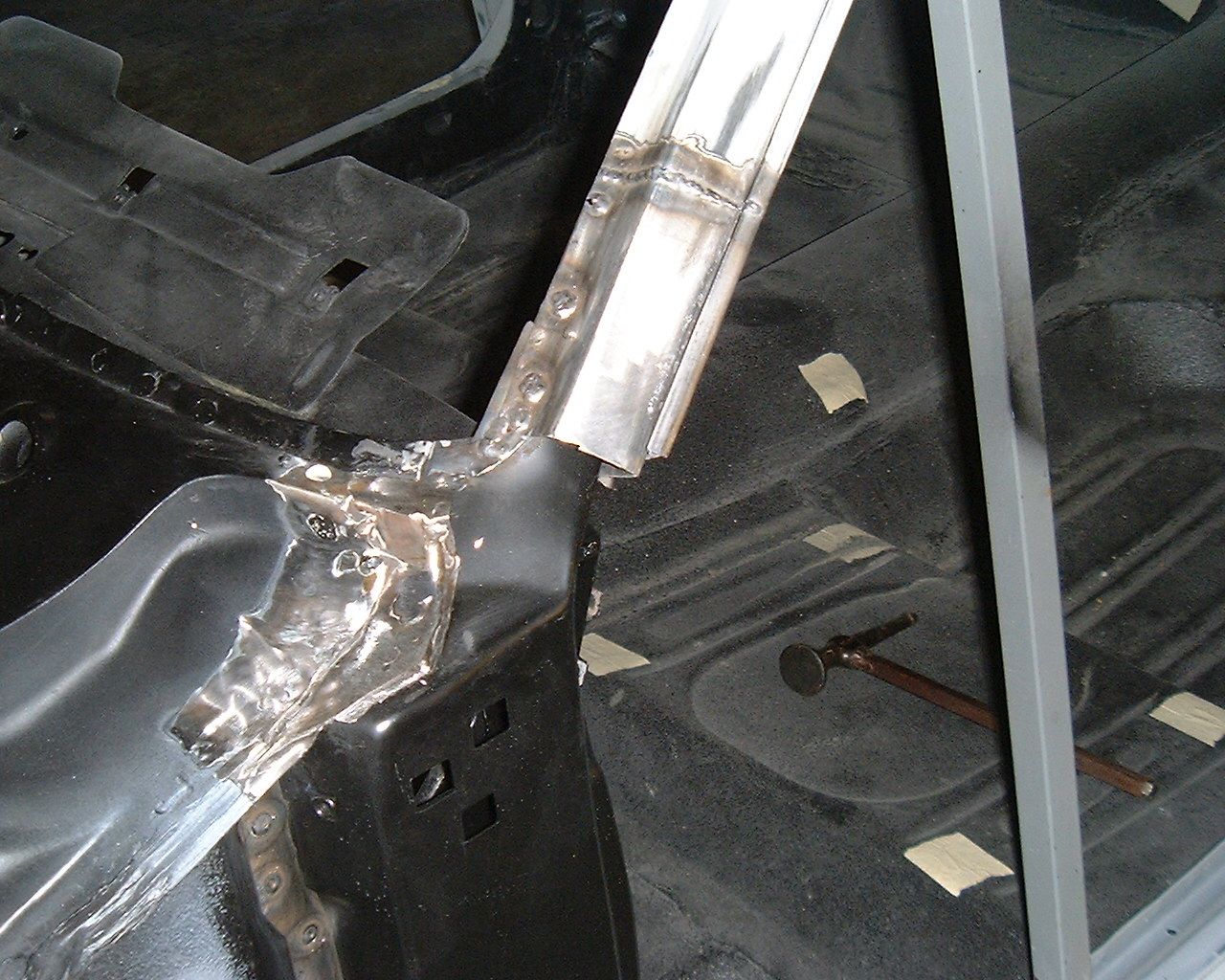
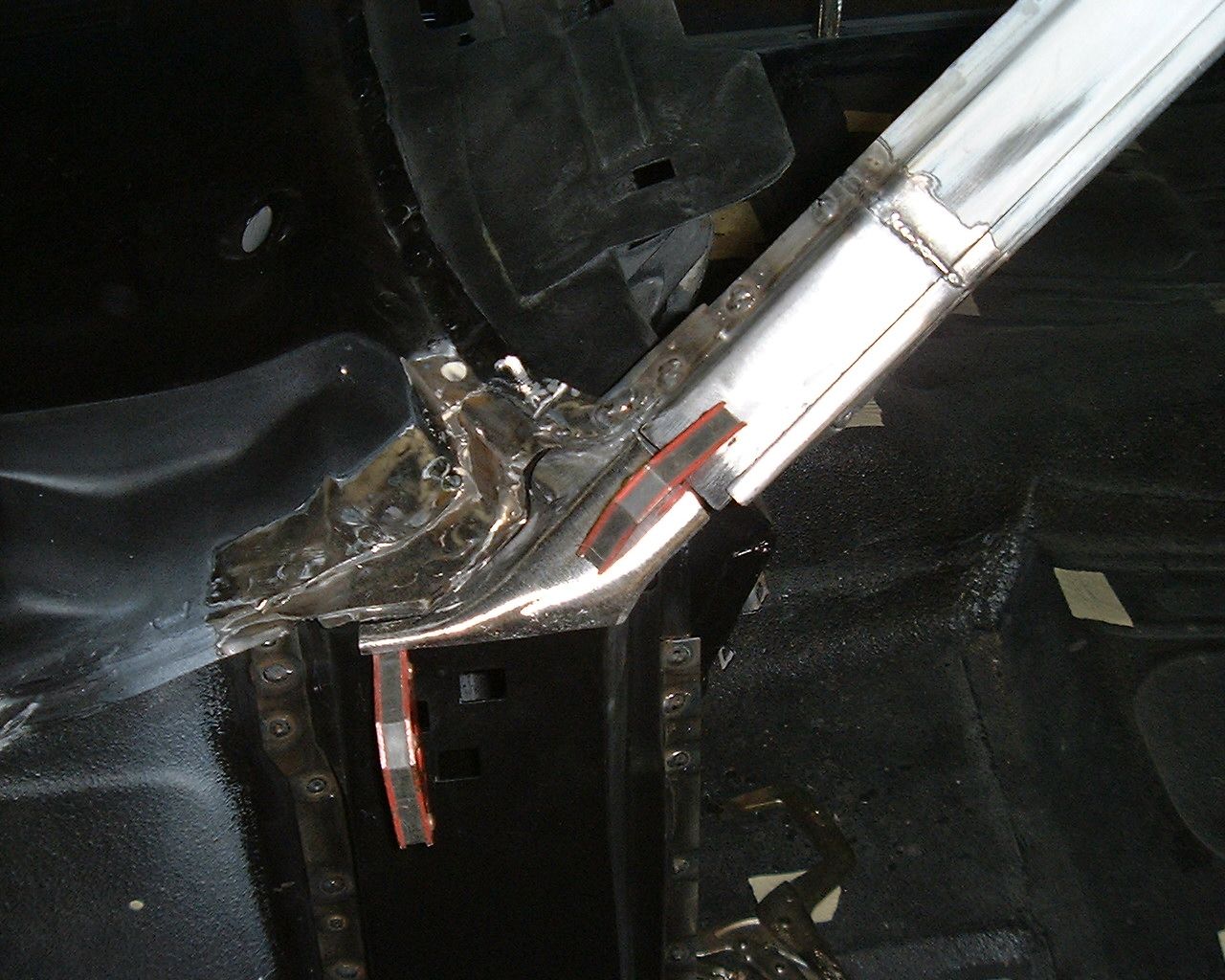
He tacked this in place and than decided he had had enough for one day and will finish on Monday.
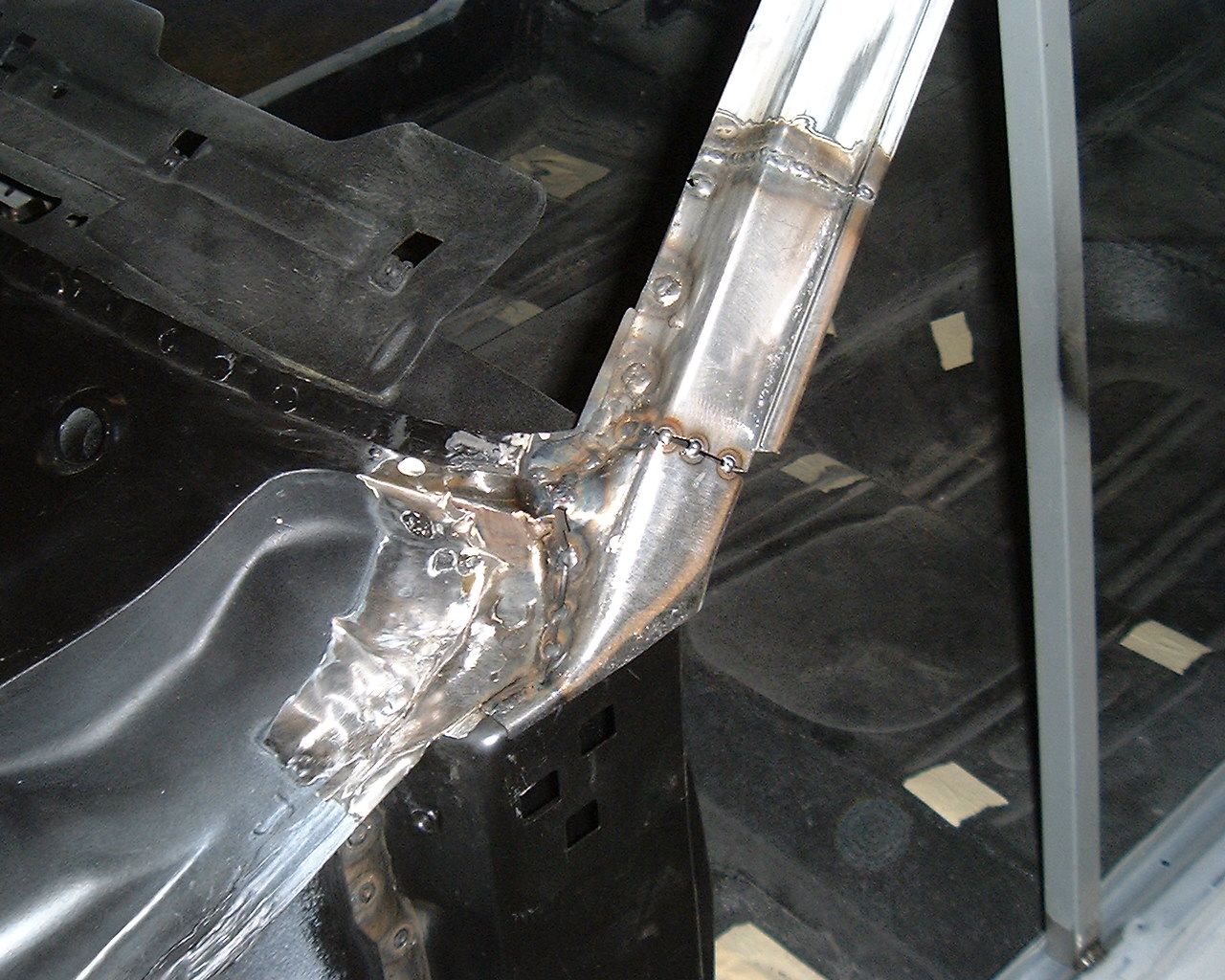